WOOD COMPOSITES
| At the forefront of testing and manufacturing new, innovative, and sustainable forest products to revitalize and diversify Maine’s forest-based economy.
WOOD COMPOSITES
At the forefront of testing and manufacturing new, innovative, and sustainable forest products to revitalize and diversify Maine’s forest-based economy.
CLIMATE SOLUTIONS
Solutions from Maine’s Forests
The ASCC’s research roots are in Wood Composites. Since its opening in 1996, the ASCC has conducted hundreds of federal and industrial trials on wood and wood-based composite materials. Prototype products such as oriented strand board (OSB), laminated strand lumber (LSL), particleboard (PB), laminated veneer lumber (LVL), glulam, plywood, and cross-laminated timber (CLT) have been manufactured and tested on-site using the ASCC’s wood composites pilot facilities.
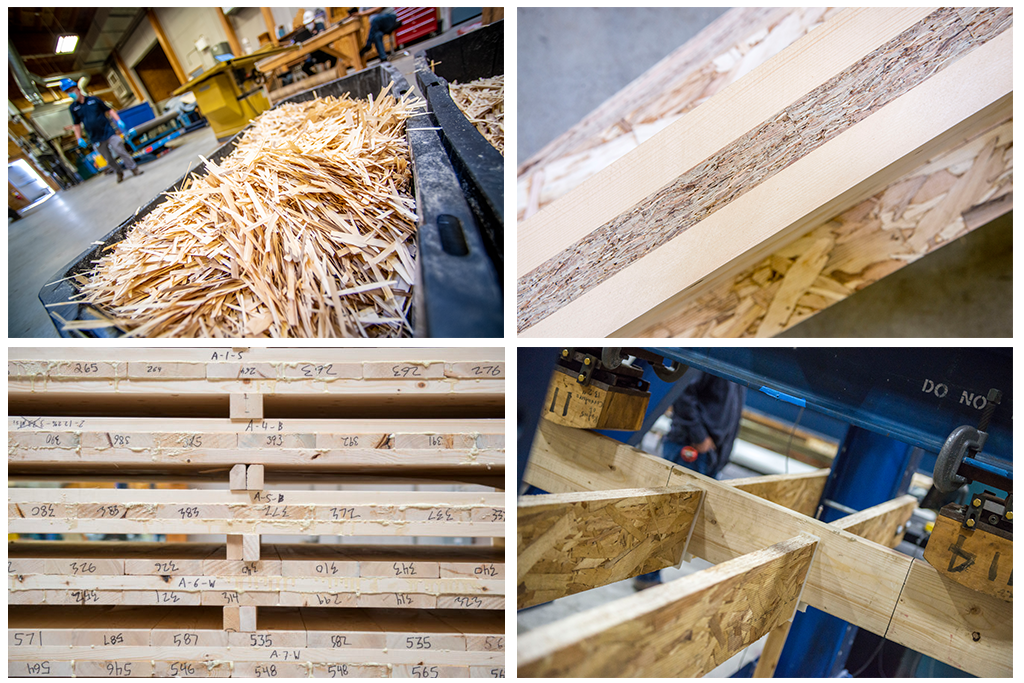
Research Areas
Mass Timber
Many architects and engineers believe that we are now in the “beginning of the timber age” where “plyscrapers” will soon be dotting city skylines all over the world. These tall wood buildings are a result of “mass timber” – a category of construction characterized by the use of large wood-based panels for wall, floor, and roof construction.
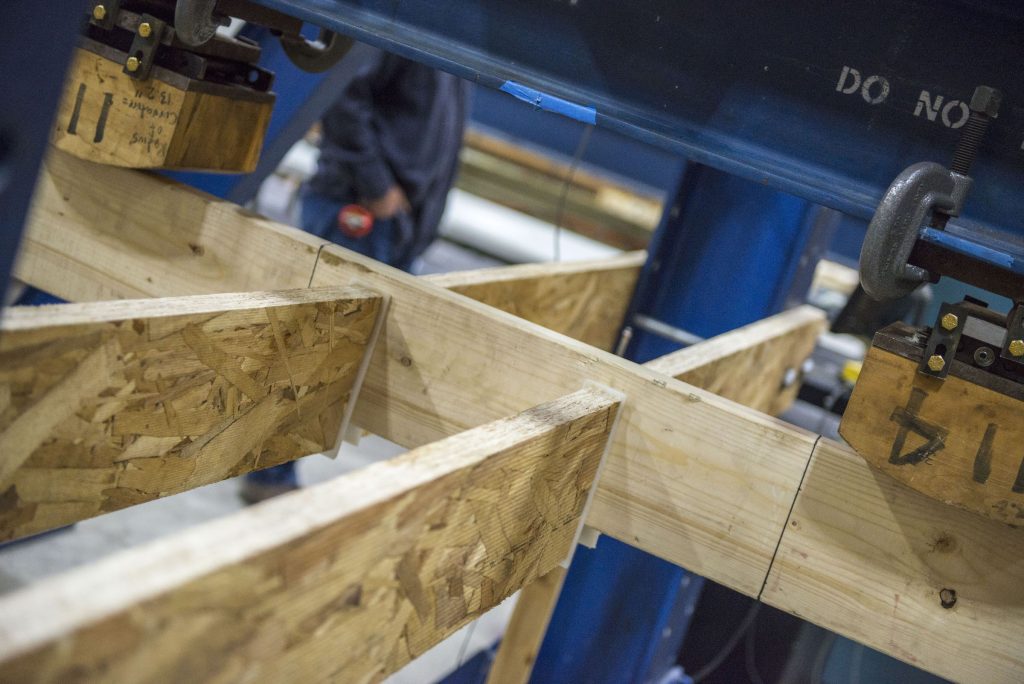
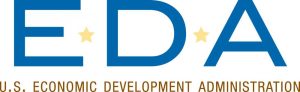
Maine Mass Timber
Commercialization Center
The MMTCC brings together industrial partners, trade organizations, construction firms, architects, and other stakeholders in the region to revitalize and diversify Maine’s forest-based economy by bringing innovative mass timber manufacturing to the State of Maine. The emergence of this new innovation-based industry cluster will result in positive economic impacts on both local and regional economies, particularly in Maine’s rural communities.
Downloadable Reports
Cross Laminated Timber
Cross Laminated Timber (CLT) is a sustainable building material that consists of multiple layers of wood boards glued together in alternating directions, providing exceptional strength and stability. The ASCC is at the forefront of pioneering research to enhance the commercial availability and sustainability of CLT in the United States.
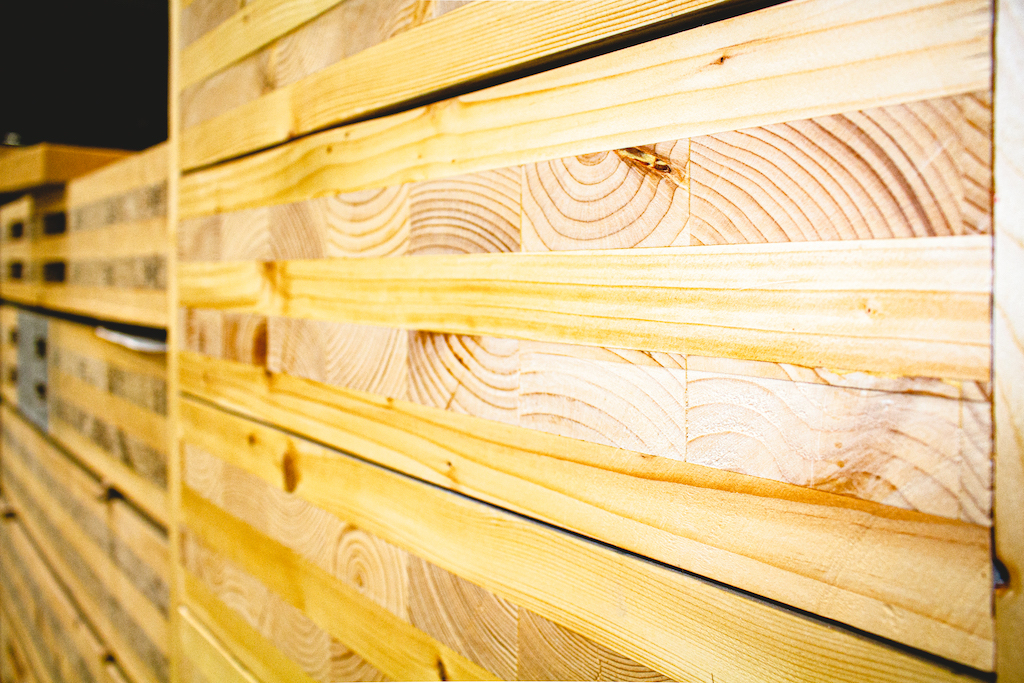
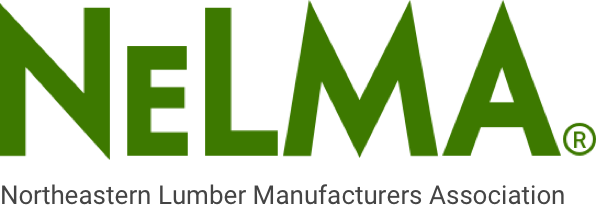
Case Study:
Norway Spruce Testing
ASCC researchers in partnership with the Northeastern Lumber Manufacturers Association (NeLMA), successfully tested and classified Norway spruce as the first new wood species for construction-grade dimensional lumber in almost a century by the American Lumber Standards Committee (ALSC).
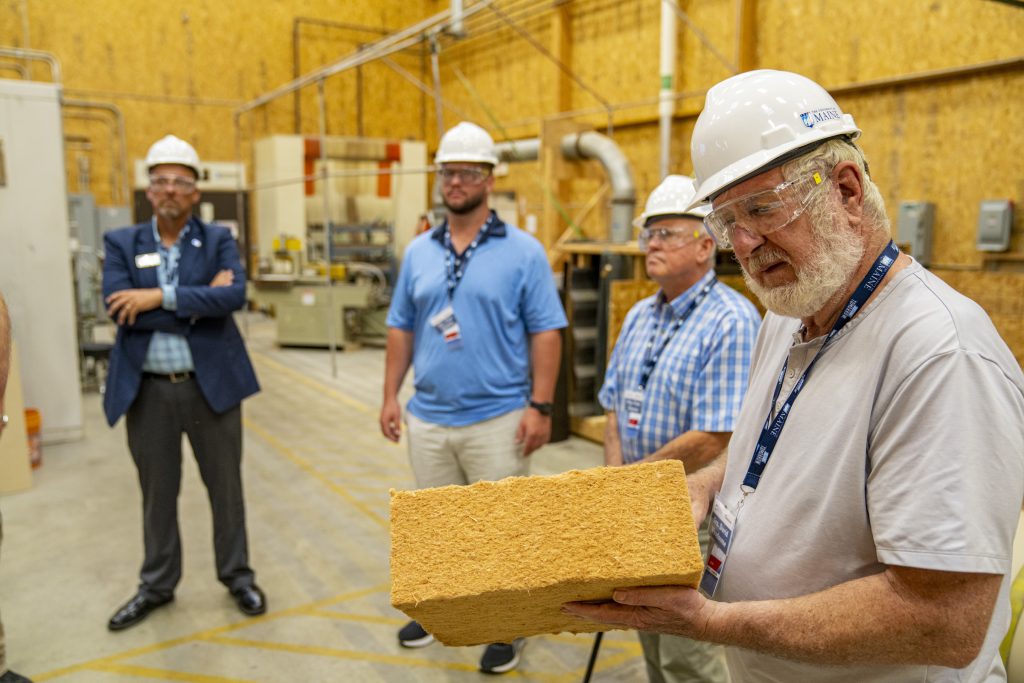
Wood Fiber Insulation
UMaine and TimberHP have partnered on R&D programs and prototyping efforts since 2018. Evaluations have investigated the effect of various manufacturing parameters, adhesives (including bio-based) type, and the investigation of the mechanical and physical properties of wood fiber insulation.
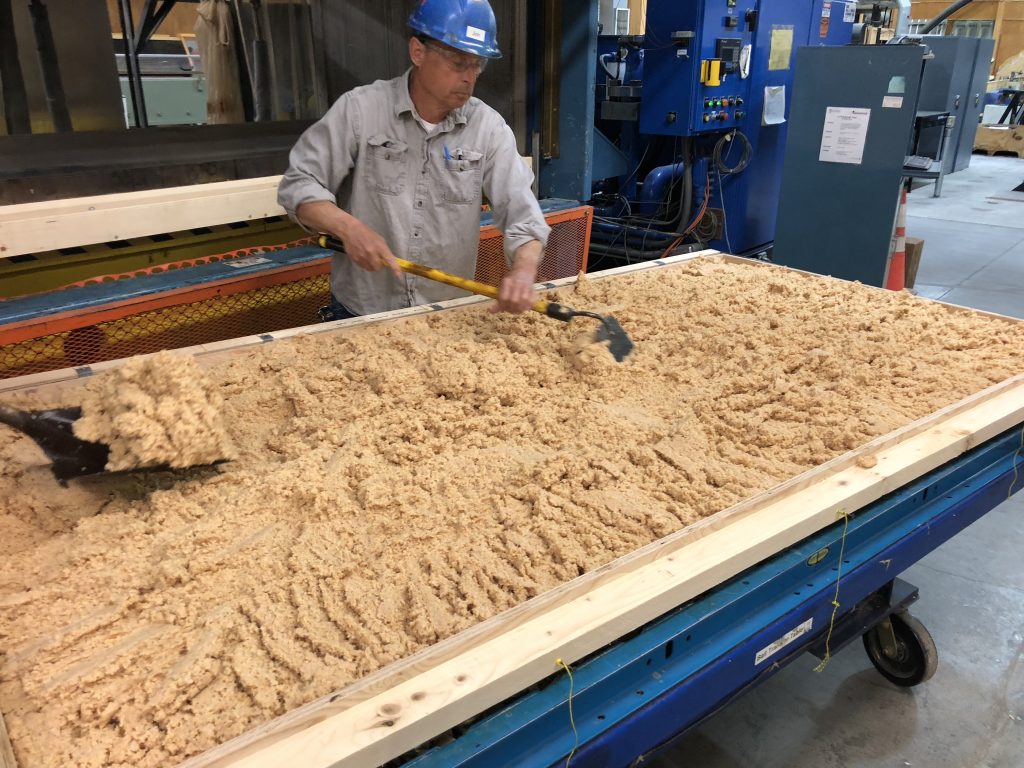