CROSS LAMINATED TIMBER
| Highly adaptable, strong and sustainable alternative to concrete.
TECHNOLOGY
Cross-laminated timber (CLT) is a mass timber product that continues to gain popularity in the U.S. after being widely adopted in Europe. CLT is the most studied mass timber product and a large focus of ASCC research.
CLT panels consist of several layers of lumber boards stacked crosswise (typically at 90 degrees) and glued together on their wide faces and, sometimes, on the narrow faces as well. Besides gluing, nails or wooden dowels can be used to attach the layers.
Cross-laminated timber used for prefabricated wall and floor panels offers many advantages. The cross-lamination process provides improved dimensional stability to the product, allowing for prefabrication of long, wide floor slabs, long single-story walls and tall plate height conditions as in multi-story balloon framed configurations. Additionally, cross-laminating provides relatively high in-plane and out-of-plane strength and stiffness properties, giving it two-way action capabilities similar to a reinforced concrete slab.
ADVANTAGES & INNOVATION
DEVELOPMENT
Qualification of two grades of CLT using Maine lumber
Researchers at UMaine recently qualified two new grades of CLT using machine stress-rated (MSR) grades of SPF-S lumber. The two grades being evaluated were “E21” utilizing 1650f-1.5E SPF-S MSR lumber in the longitudinal layers and “E21M1” utilizing 2100f-1.8E SPF-S MSR lumber in the longitudinal layers. Both of these grades utilize No. 3 SPF-S lumber in the transverse layers.
Four units of 2100f-1.8E SPF-S MSR 2×6 lumber from Maibec Lumber Co. (Masardis, Maine), and 7 units of PMO SPF-S 2×6 lumber from Pleasant River Lumber Co. (Moose River, Maine), were shipped to SmartLam, LLC (Columbia Falls, Montana) for conditioning and CLT manufacturing. After CLT manufacturing and specimen preparation, materials were shipped to the University of Maine’s Advanced Structures and Composites Center (ASCC) for testing under ANSI/APA PRG 320, Standard for Performance-Rated Cross-Laminated Timber.
The test data justified the design values for the CLT grades, with the CLT specimens passing all testing – usually by a healthy margin. The study concluded that both of the new E21 and E21M1 grades of CLT are qualified for used.
The E21M1 grade has the highest published bending properties in the longitudinal direction of any CLT grade currently listed in PRG 320, while the E21 grade is comparable to “E2” grade CLT, which is manufactured with Douglas-fir, a species known for its high stiffness and strength. Introduction of these grades to those currently available in North America (or globally) derisks investment of CLT manufacturing in Maine and New England.
Bonding quality testing of SPF-S lumber for CLT
Unlike nail-laminated timber and dowel-laminated timber, adhesive bonds are typically used in the manufacturing of CLT and Glulam. These adhesives are responsible for transferring loads and providing durable bonds during the structure’s service life.
All species in the SPF-S grouping, as well as white pine and eastern hemlock, demonstrated compliance with the face-bond acceptance criteria for North America.
Recently researchers at UMaine evaluated the bonding performance of all the SPF-S species as well as two other commercially viable softwood species in the northeast: white pine and eastern hemlock when used in CLT, to the acceptance criteria included in PRG 320.
The testing concluded that from a bonding perspective, all species in the SPF-S grouping, and eastern hemlock and white pine, are acceptable lamstock for CLT production.
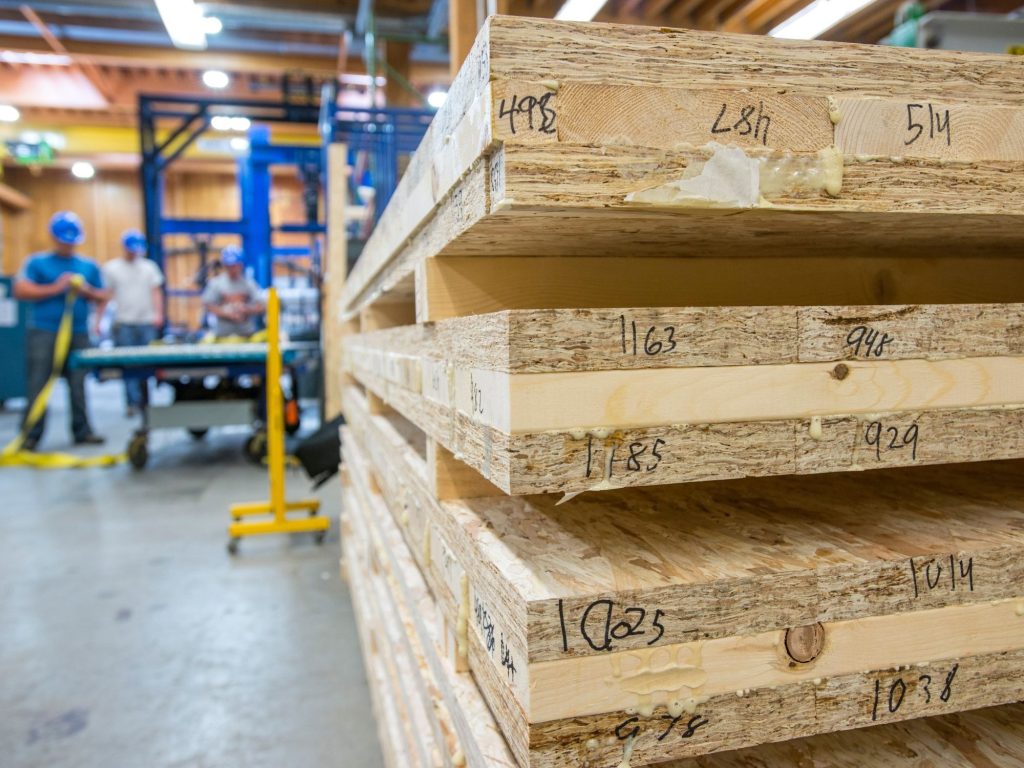
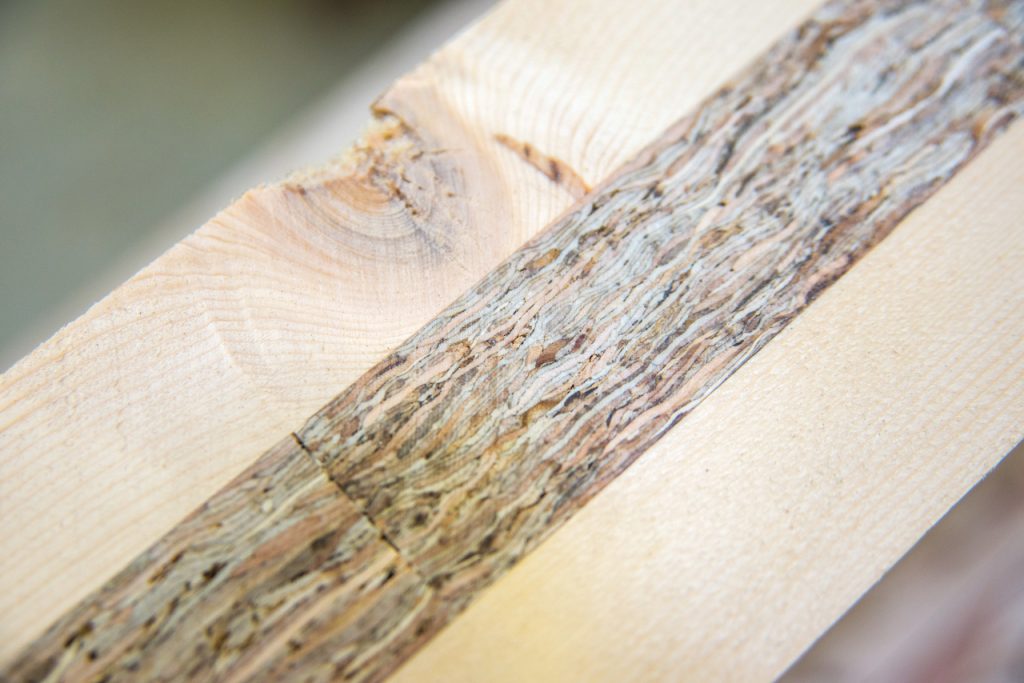
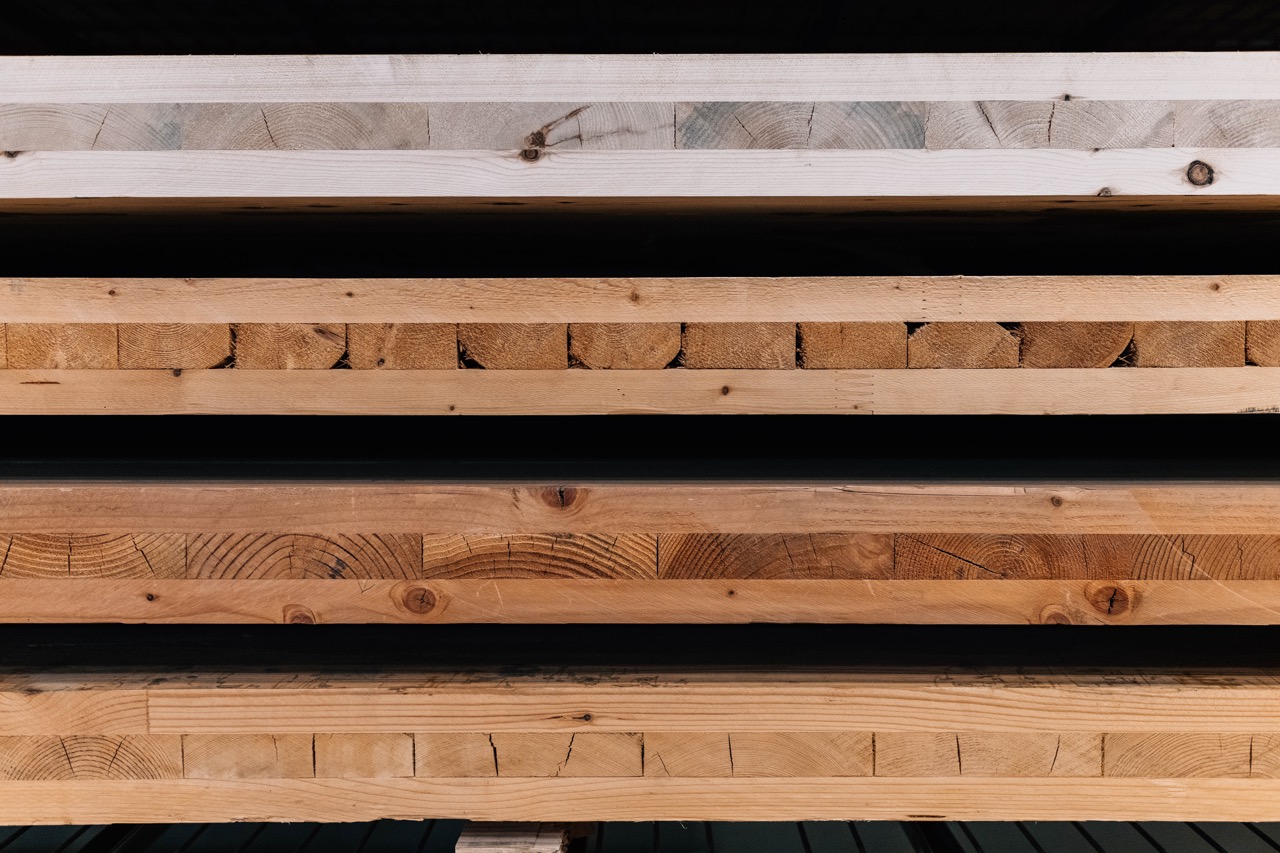
