A 1:50-scale marine model testing facility that accurately simulates towing tests, variable water depths, and scaled wind and wave conditions that represent some of the worst storms possible anywhere on Earth
CAPABILITIES
EQUIPMENT
The W2
In 2015, the Center received its largest philanthropic gift to date from the Harold Alfond Foundation to name the $13.8 million Alfond W2 Ocean Engineering and Advanced Manufacturing Labs.
Wave Basin
Multi-directional Wave Generator
Towing System
Wind Generator
In-House Model Design and Fabrication Capabilities
Instrumentation
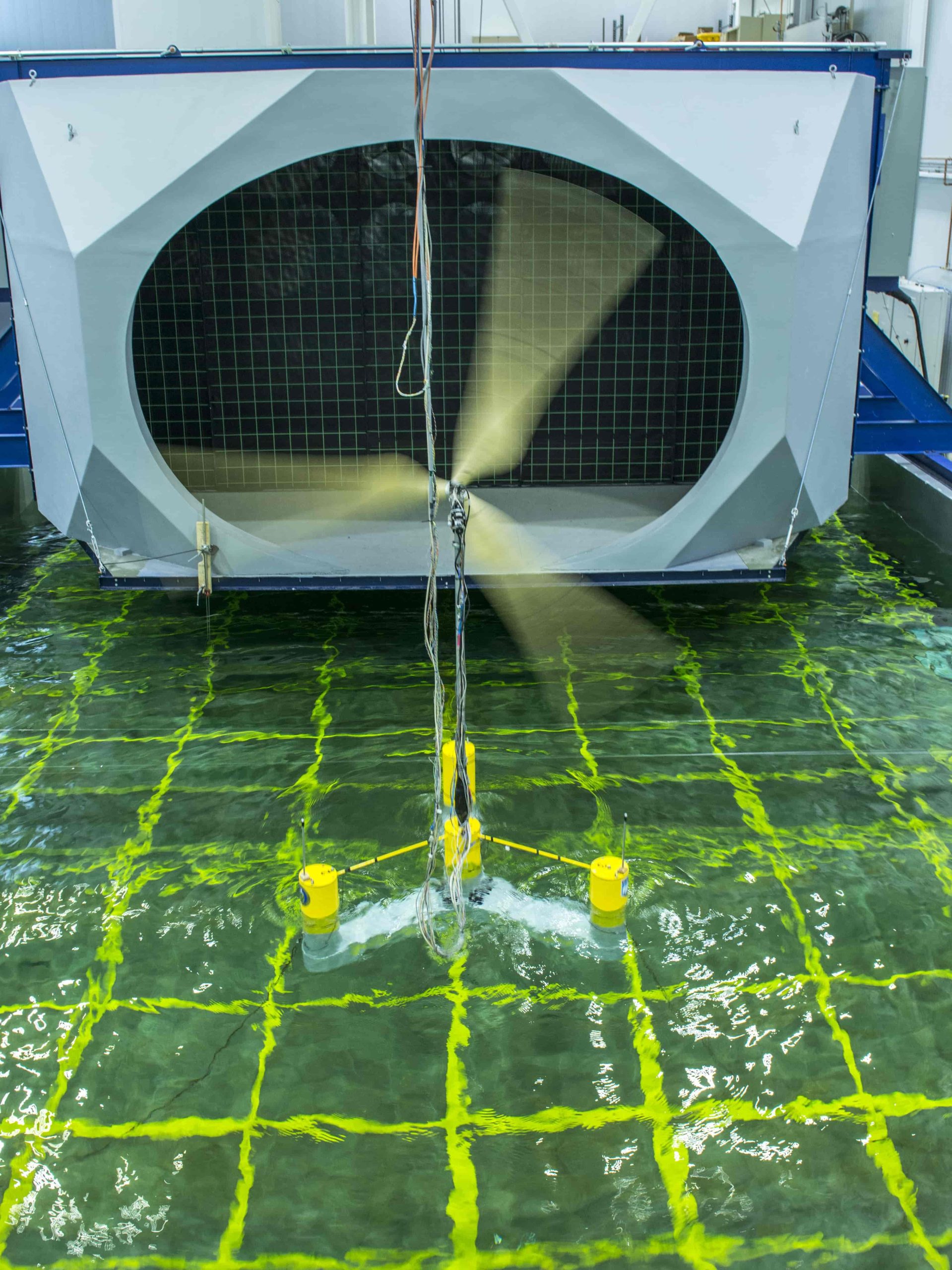
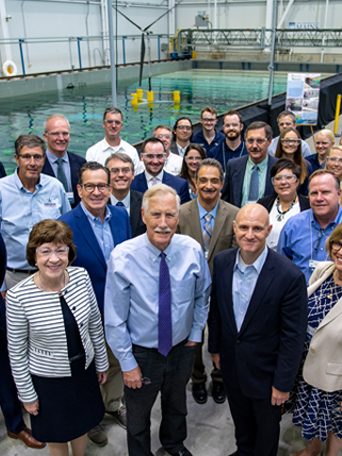
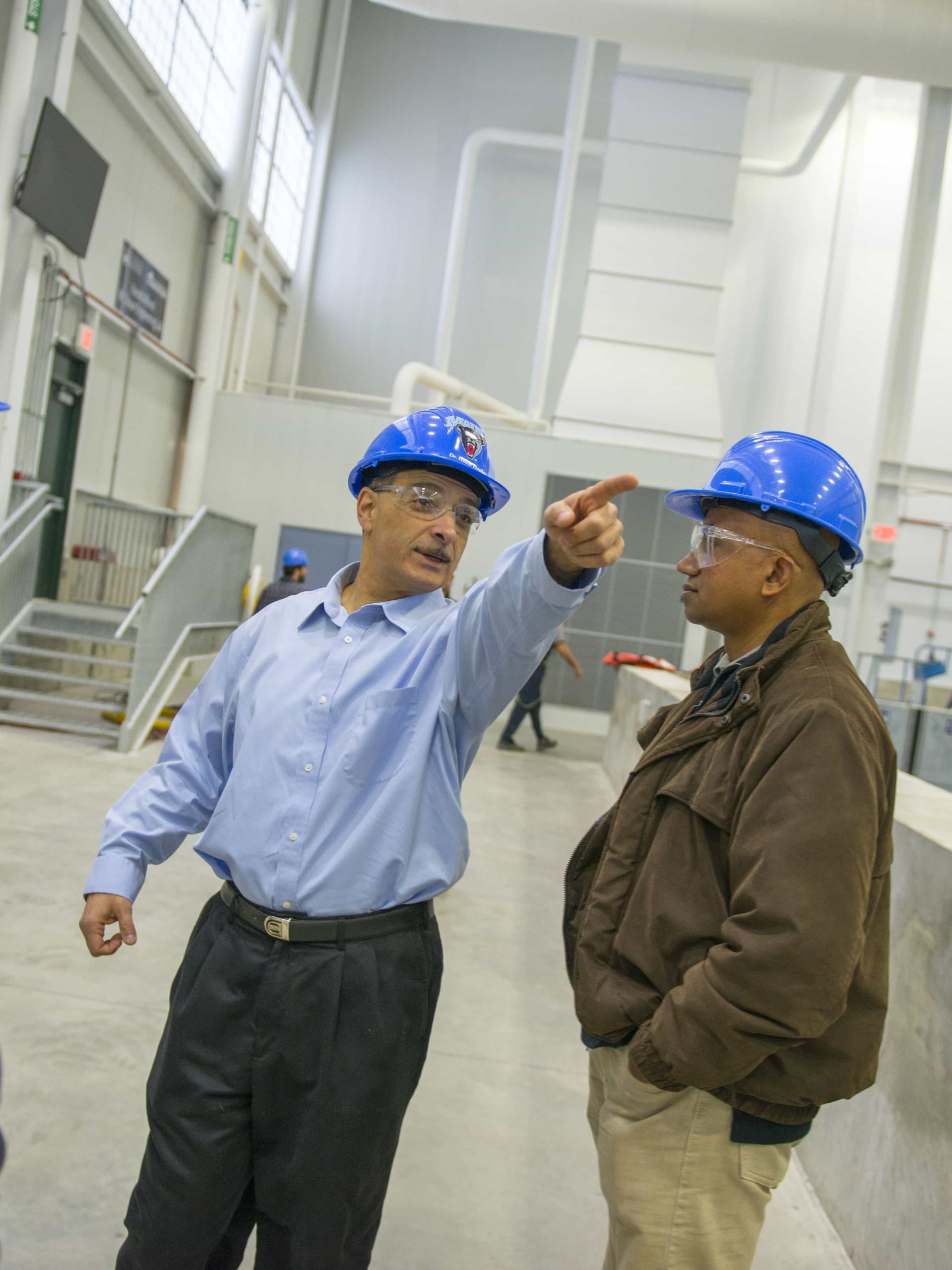
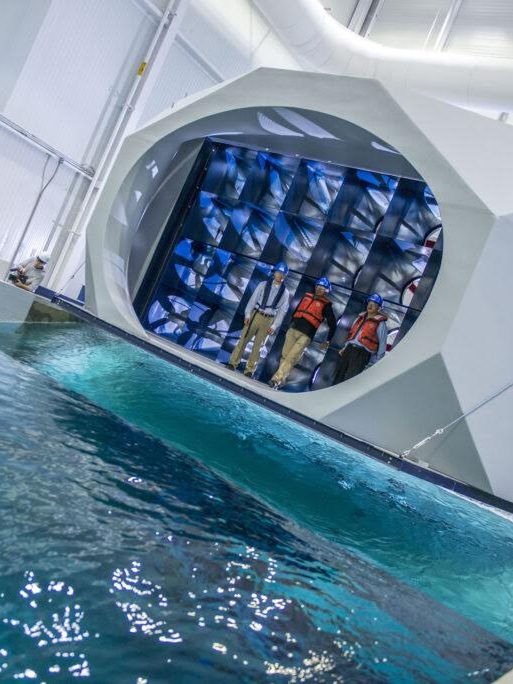
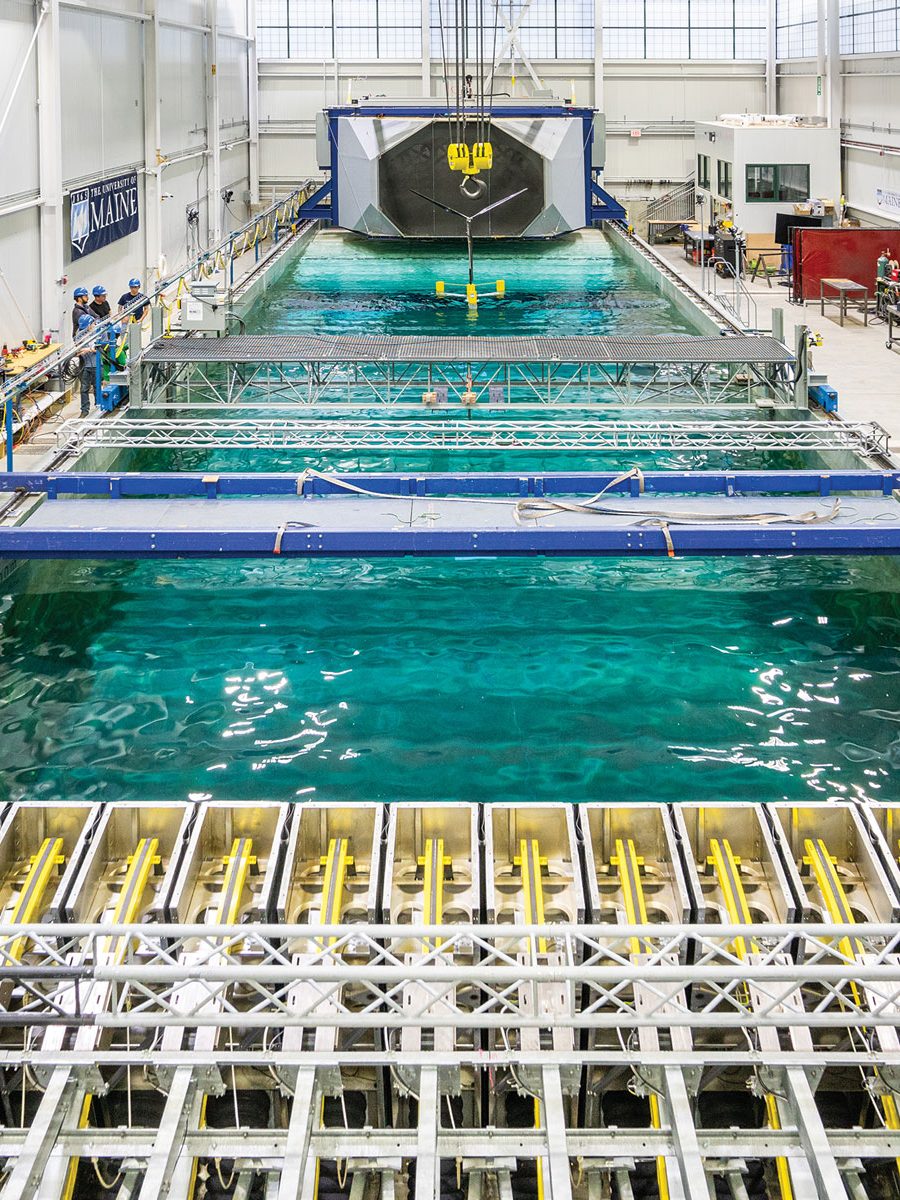
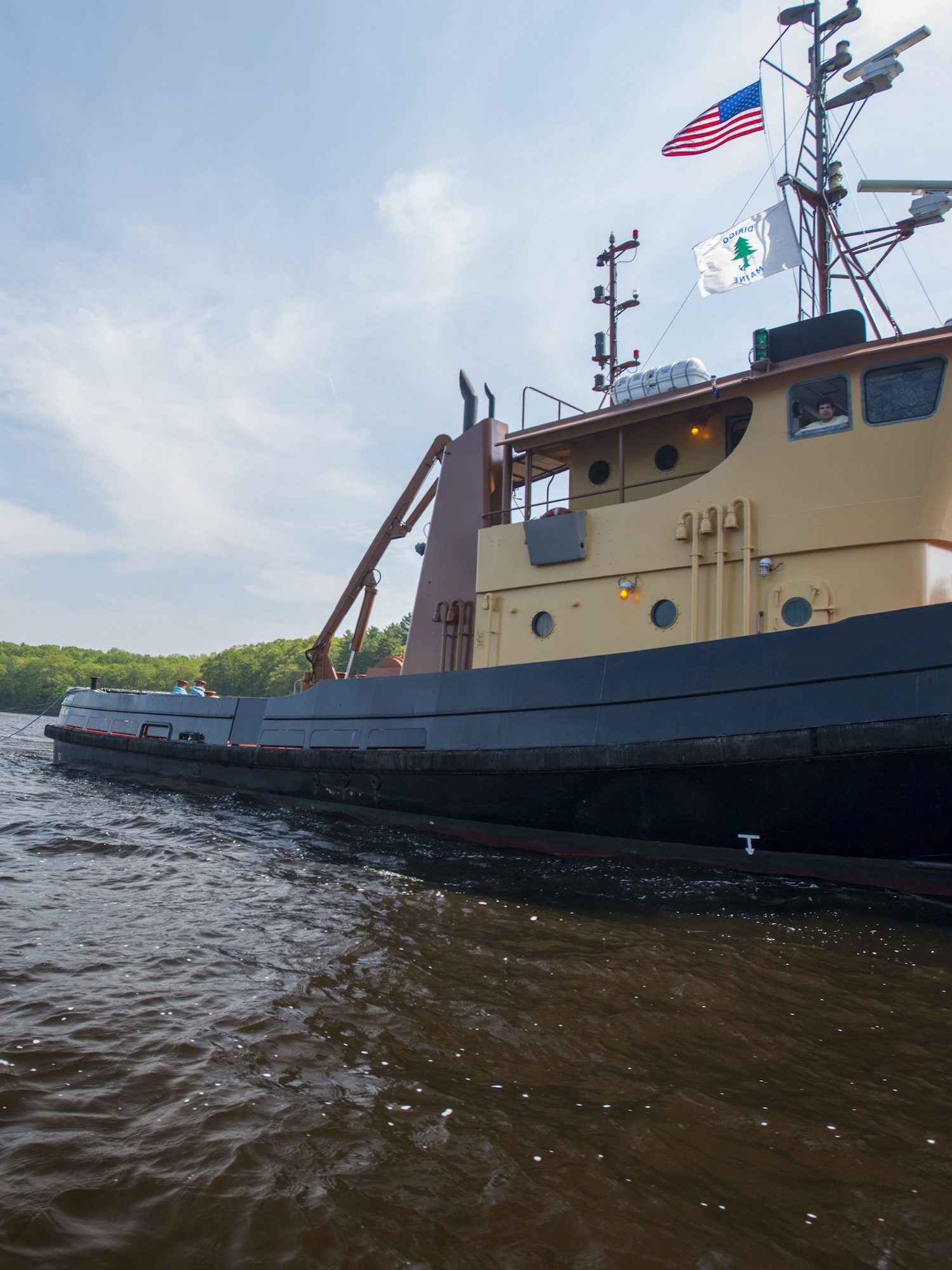