Structural Thermoplastics
Structural Thermoplastics
Alfond Advanced Manufacturing Lab for Structural Thermoplastics
The Alfond Advanced Manufacturing Laboratory for Structural Thermoplastics accelerates manufacturing with digital, additive, and robotics technologies to cut costs and cycle times. Thermoplastic composites are lightweight, recyclable, corrosion-resistant, and strong enough for structural applications in defense, automotive, aerospace, marine, and consumer goods.
ASCC’s state-of-the-art lab features 3D printing, thermoforming, a fast-reaction molding press, an advanced tape layup machine, and a dual robotic manufacturing cell. In partnership with industry, it drives thermoplastic research, testing, and workforce training.
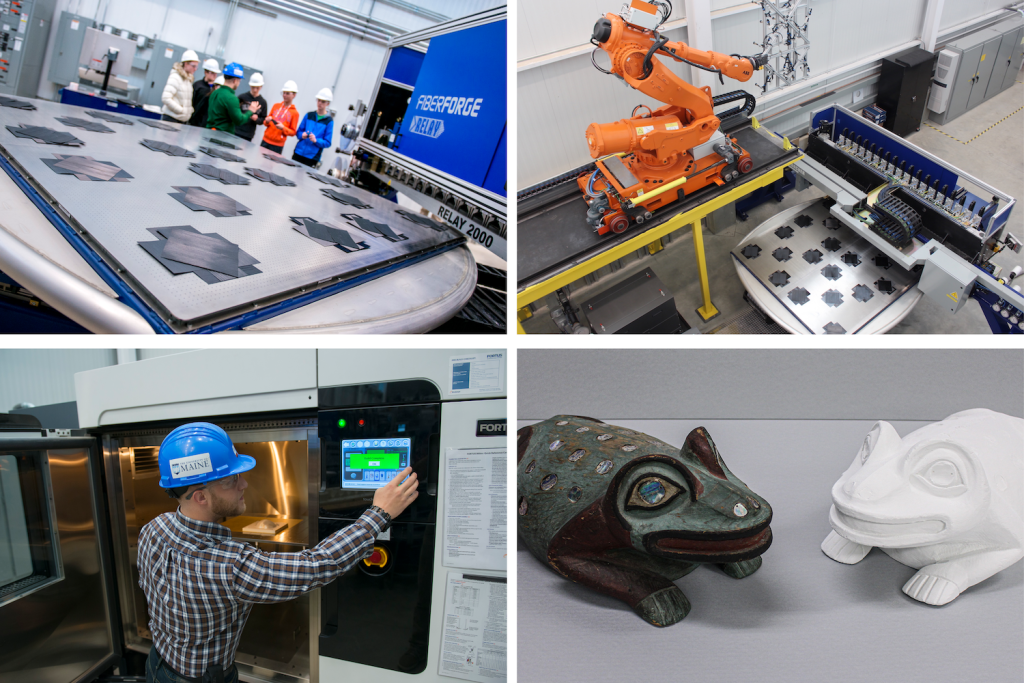
/
Rapid Prototyping Development
We work with corporations, government agencies, and academic institutions of all sizes to partner on research, development, and commercialization projects, such as:
- Manufacturing process and tooling design and development
- Proof of concept demonstration and economic analysis
- Reengineering metals and thermosets into thermoplastic composites
- Joint U.S. research and development funding opportunities
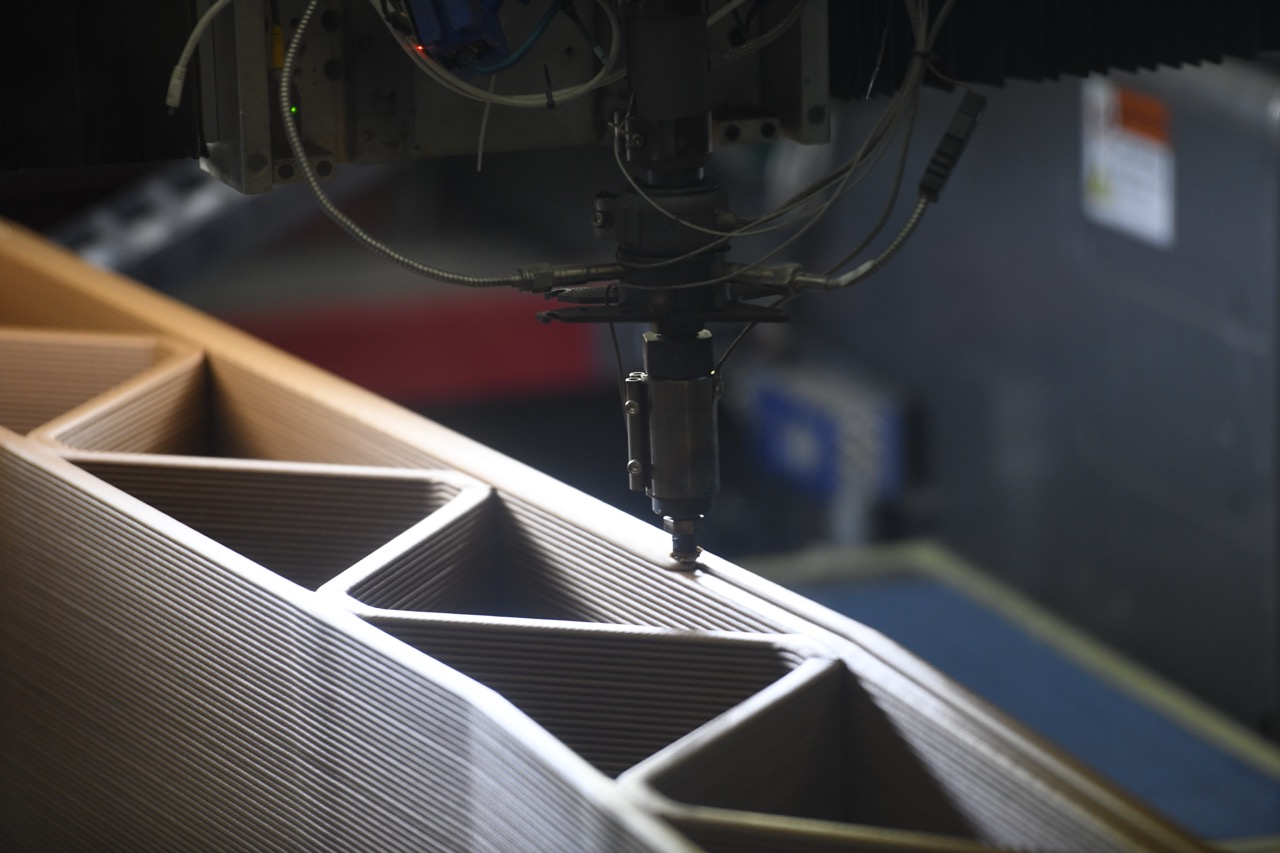
Facilities and Capabilities
Offering industry partnerships for process development, material testing, and commercialization.