MATERIAL DEVELOPMENT & CHARACTERIZATION
FACILITIES + CAPABILITIES
MATERIAL DEVELOPMENT & CHARACTERIZATION
FACILITIES + CAPABILITIES
Work with our world-class material testing team and facilities.
Plastic Materials
- ASTM D256 Determining the Izod Pendulum Impact Resistance of Plastics
- ASTM D635 Rate of Burning and/or Extent and Time of Burning of Plastics in a Horizontal Position
- ASTM D638 Tensile Properties of Plastics
- ASTM D695 Compressive Properties of Rigid Plastics
- ASTM D696 Coefficient of Linear Thermal Expansion of Plastics Between -30 °C and 30 °C with a Vitreous Silica Dilatometer
- ASTM D790 Flexural Properties of Unreinforced and Reinforced Plastics and Electrical Insulating Materials
- ASTM D792 Density and Specific Gravity (Relative Density) of Plastics by Displacement
- ASTM D953 Bearing Strength of Plastics
- ASTM D2765 Standard Test Methods for Determination of Gel Content and Swell Ratio of Crosslinked Ethylene Plastics
- (Methods A and C)
- ASTM D3846 In-plane Shear Strength of Reinforced Plastics
- ASTM D4065 Standard Practice for Plastics: Dynamic Mechanical Properties: Determination and Report of Procedures
- ASTM D4812 Unnotched Cantilever Beam Impact Strength of Plastics
- ASTM D6109 Flexural Properties of Unreinforced and Reinforced Plastic Lumber
- ASTM D6110 Determining the Charpy Impact Resistance of Notched Specimens of Plastics
Composite Materials
- ASTM C393 Flexural Properties of Sandwich Constructions
- ASTM D2344 Short-beam Strength of Polymer Matrix Composite Materials and Their Laminates
- ASTM D2584 Ignition Loss of Cured Reinforced Resins
- ASTM D3039 Tensile Properties of Polymer Matrix Composite Materials
- ASTM D3410 Compressive Properties of Polymer Matrix Composite Materials with Unsupported Gage Section by Shear Loading
- ASTM D3479 Tension-Tension Fatigue of Polymer Matrix Composite Materials
- ASTM D3518 In-plane Shear Response of Polymer Matrix Composite Materials by Tensile Test of a ± 45o Laminate
- ASTM D4255 Standard Guide for Testing In-plane Shear Properties of Composite Laminates
- ASTM D6115 Mode I Fatigue Delamination Growth Onset of Unidirectional Fiber-Reinforced Polymer Matrix Composites
- ASTM D6641 Compressive Properties of Composite Laminates Using a Combined Loading Compression (CLC) Fixture
- ASTM F1679 Using a Variable Incidence Tribometer (VIT)
Adhesive Materials
- ASTM D905 Strength Properties of Adhesive Bonds in Shear by Compression Loading
- ASTM D1101 Integrity of Adhesive Joints in Structural Laminated Wood Products for Exterior Use
- ASTM D2339 Strength Properties of Adhesives in Two-Ply Wood Construction in Shear by Tension Loading
- ASTM D2559 Standard Specification for Adhesives for Structural Laminated Wood Products for Use Under Exterior (Wet Use) Exposure Conditions
- ASTM D3165 Strength Properties of Adhesives in Shear by Tension Loading of Single-Lap-Joint Laminated Assemblies
Material Coupon Testing
Servohydraulic tension-compression test frames
- 1 x 500 kN capacity
- 3 x 100 kN capacity
- 1 x 25 kN capacity
Servohydraulic tension-compression test frames
- 1 x 100 kN / 1100 N·m capacity
- 1 x 25 kN / 100 N·m capacity
- Drop weight impact testing machine, 1.5-1250 J
Non-Destructive Testing
- Phased-array ultrasonic inspection
- Acoustic emission testing
- Embedded fiber optic strain sensing
Microscopy
- Optical microscopy
- Scanning electron microscopy (SEM)
- Environmental SEM
- Transmission electron microscopy (TEM)
- Atomic force microscopy (AFM)
- Microtomography
- Laser scanning confocal microscopy (LSCM)
CONTACT:
Matthew Ayotte
|Instrumentation Manager
matthew.AYOTTE@composites.maine.edu
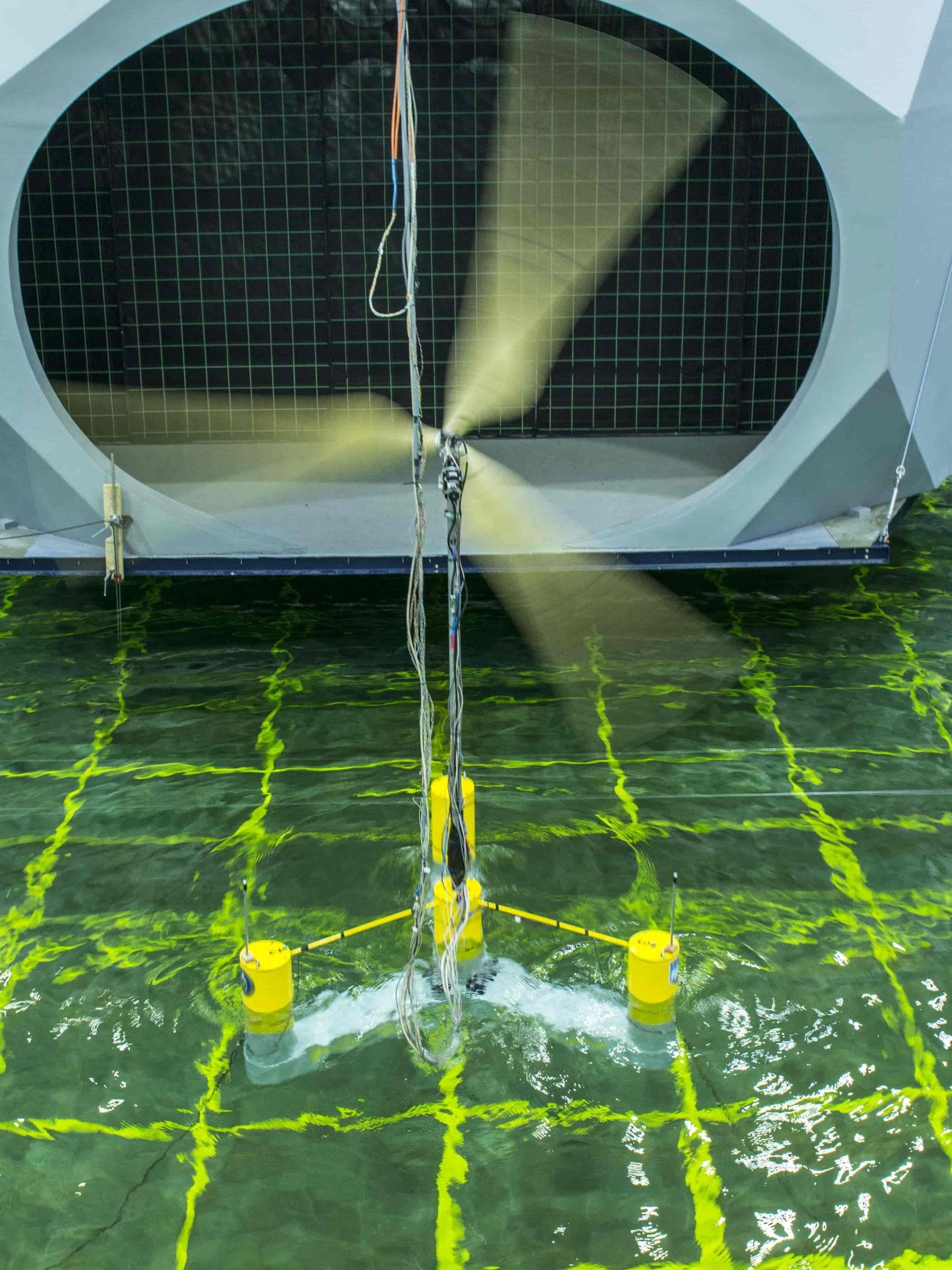
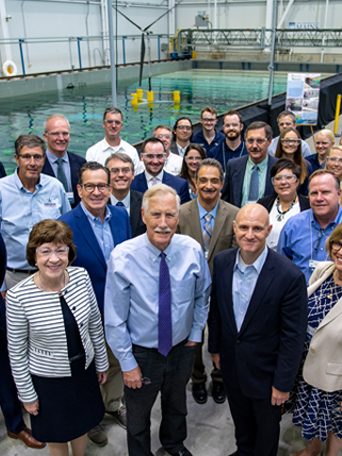
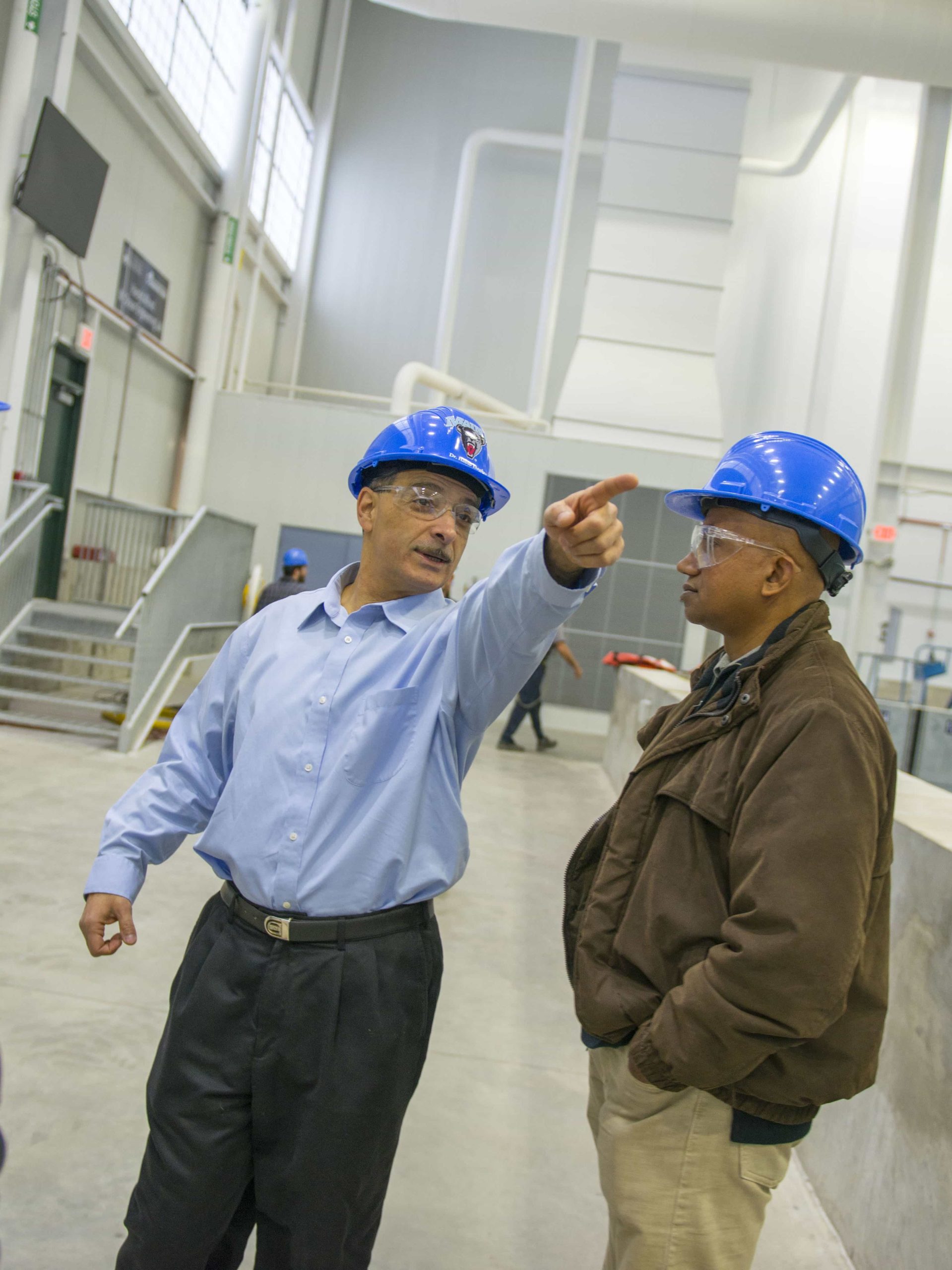
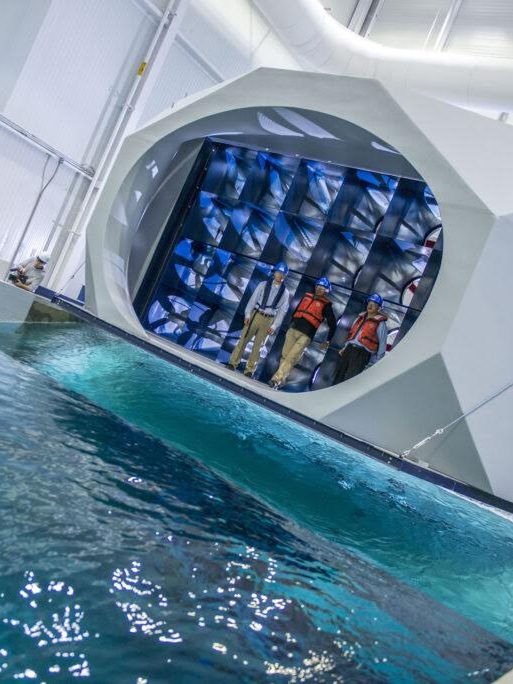
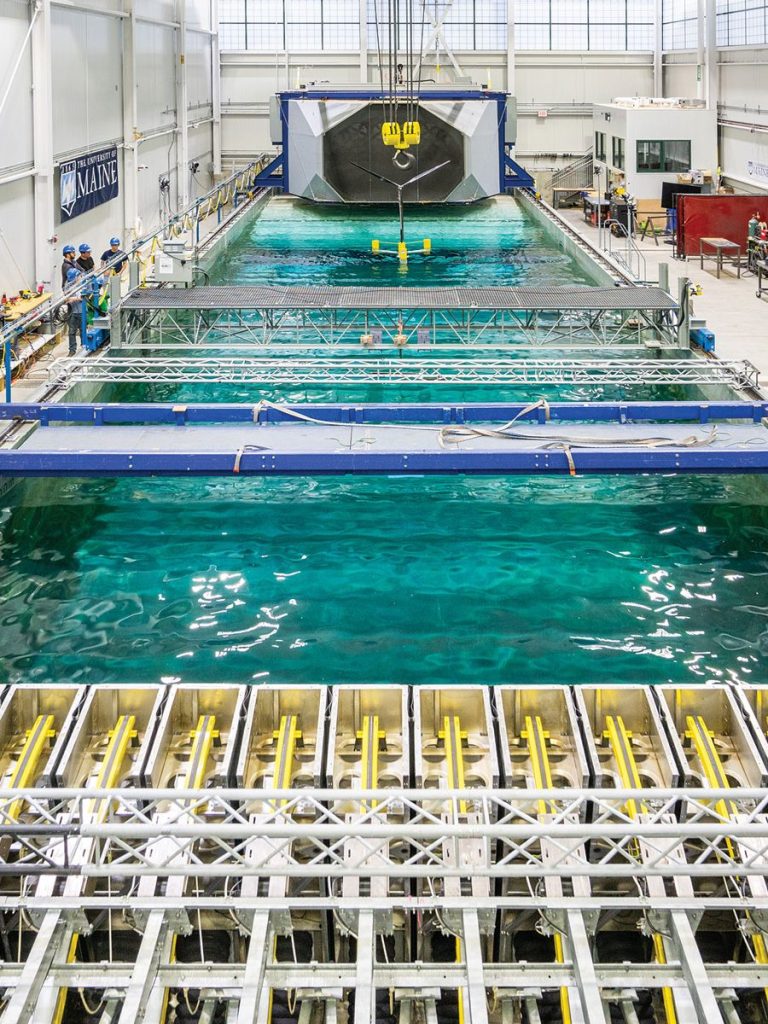
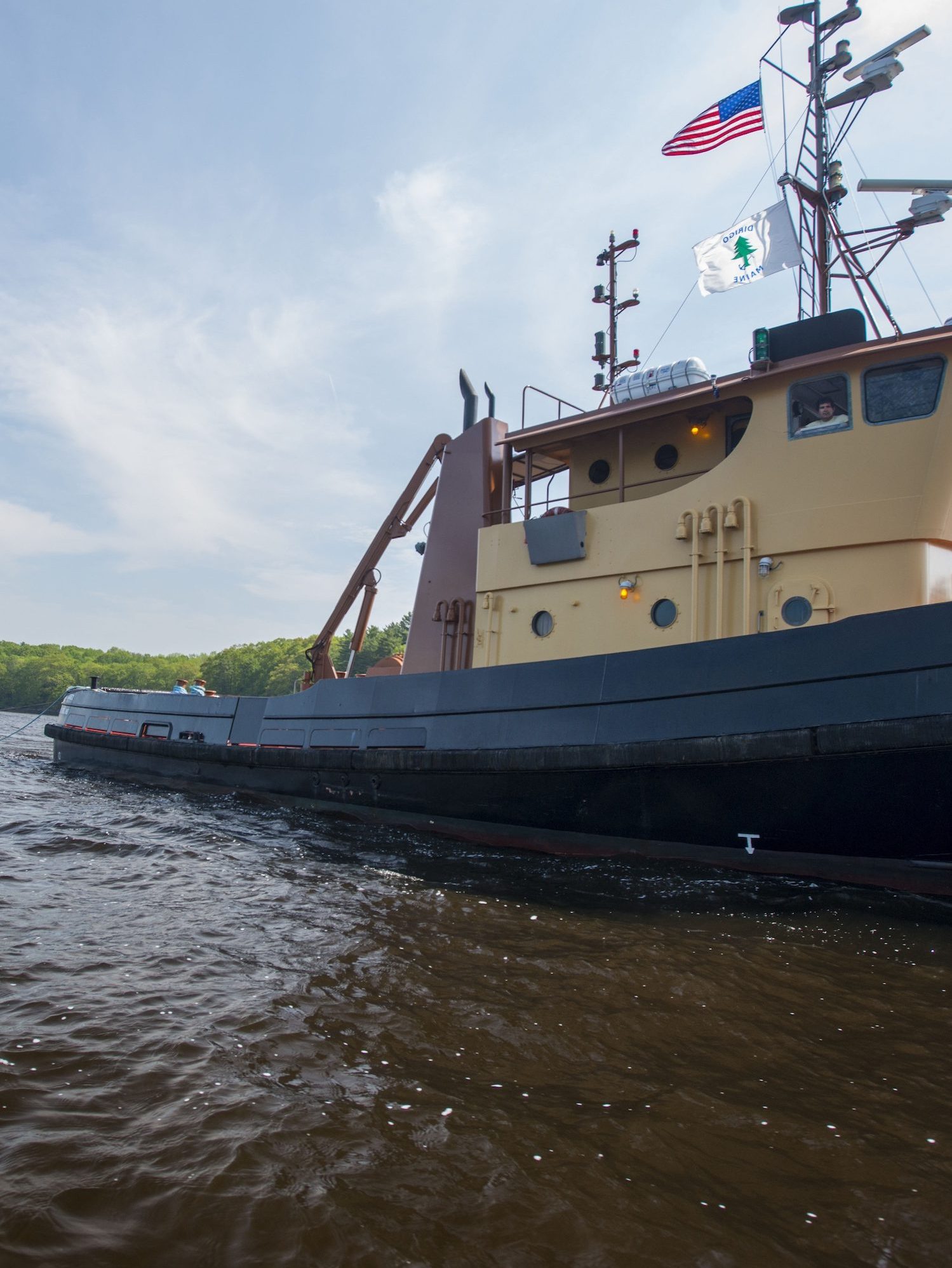