NATIONAL SECURITY
| National leaders in advanced manufacturing, delivering cutting-edge solutions in design, testing, and deployment to safeguard U.S. security interests across marine, infrastructure, defense, and space sectors through pioneering research and technology transition.
NATIONAL SECURITY
National leaders in advanced manufacturing, delivering cutting-edge solutions in design, testing, and deployment to safeguard U.S. security interests across marine, infrastructure, defense, and space sectors through pioneering research and technology transition.
DEFENSE SOLUTIONS
National Security from the ASCC
The ASCC is a hub of research and development with expertise in design, manufacturing, testing and deploying, committed to bolstering national security throughout our research portfolio. With a focus on marine, infrastructure, defense, space sectors and more, the ASCC’s innovative initiatives have far-reaching implications for safeguarding critical aspects of our nation’s interests. From advancing vessel structures and composite tooling development in the marine industry to spearheading forward manufacturing technologies for Expeditionary Advanced Base Operations (EABO) in defense, the ASCC’s interdisciplinary approach drives groundbreaking solutions tailored to meet the complex challenges of the modern security landscape. By developing technologies to meet the critical needs of the Department of Defense (DoD), we also lay the groundwork for their transition into technologies that support civilian needs. This strategic approach not only enhances national security but contributes to advancements that benefit society at large.
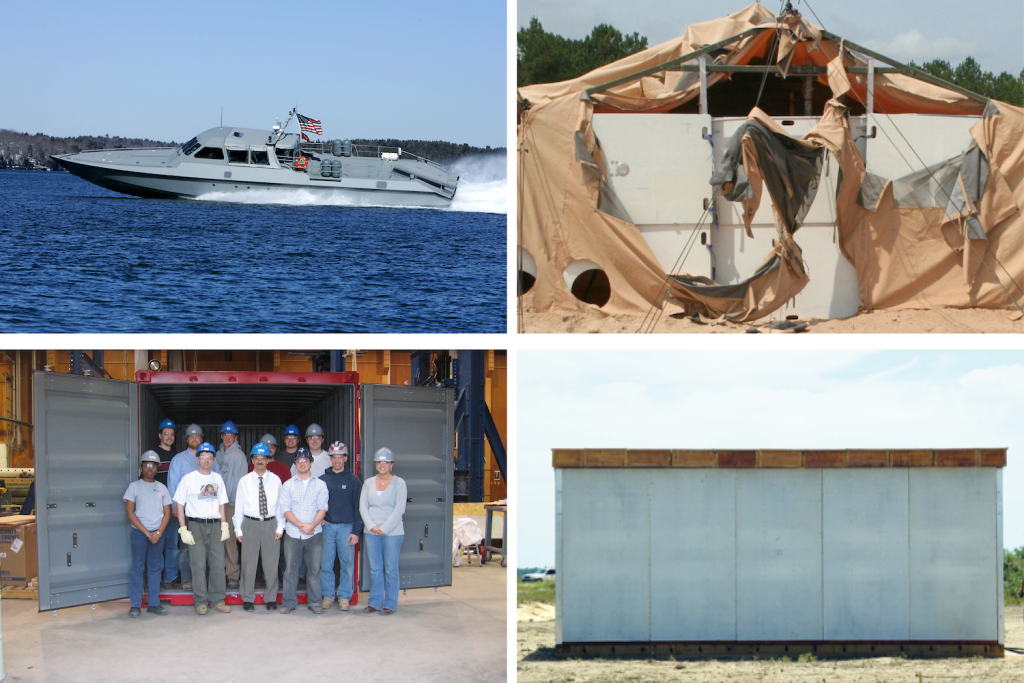
Research Areas
Modular Ballistic Protection System (MBPS)
MBPS, developed in partnership with the US Army Natick Soldier RD&E Center, provides soldiers with enhanced ballistic protection in the field where it never existed before.
MBPS is a quickly erectable, re-deployable, and lightweight ballistic protection system. MBPS provides ballistic protection for personnel and equipment in expeditionary base camps where mobility and rapid deployment requirements prevent the immediate use of heavyweight systems like sandbags and concrete barriers. MBPS requires no tools to up-armor a standard-issue 20 ft x 32 ft tent and can be deployed in less than 30 minutes by 4 soldiers.

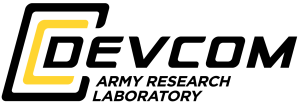
Origami Structures
In partnership with The U.S. Army Combat Capabilities Development Command Soldier Center, this research is looking at the design of rapidly deployable shelters with rigid flat panels that must fold and unfold in a kinematically compliant fashion.
MAKO
Designed in partnership with Hodgdon Defense Composites and Maine Marine Manufacturing, the UMaine Composites Center performed testing on a special operations boat with a fully composite hull to replace the aluminum hull craft currently used by the US Navy Seals. This 83-foot-long, impact-resistant prototype is the result of a $15 million research and development project that resulted in the first all-composites hull for the US Navy.
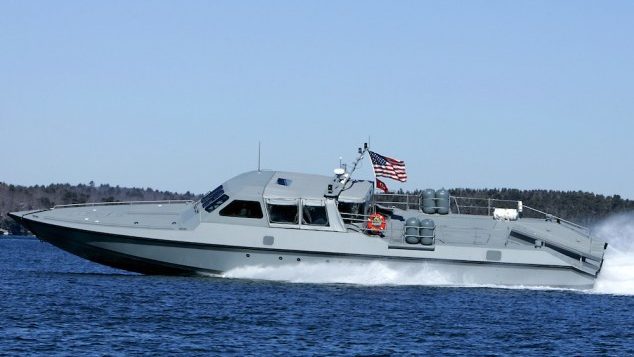
Blast Resistant Structures
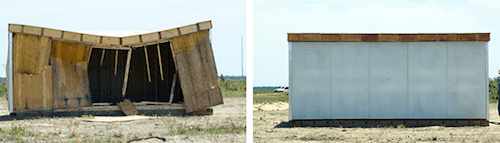
In partnership with the U.S. Army Corps of Engineers ERDC, the UMaine Composites Center developed blast-resistant structures with coated wood framing members, panels, and subassemblies. These blast-resistant materials are economically coated to enhance the construction material’s ductility and energy dissipation capacity.
In addition to superior blast resistance, benefits of these structures include cost-efficiencies, ease of assembly, environmental durability, rapid deployment, high strength to weight ratios, and protection from moisture absorption, termites, ants, and biodegradation. The images to the left show Conventional construction (left) vs the last Resistant Modular Construction (right) after truck bomb equivalent.
Lightweight Military Ground Vehicles (LMGV)
A partnership with the ASCC and US Army DEVCOM Ground Vehicle System Center was formed to develop technology to reduce the weight of military ground vehicles with fiber-reinforced thermoplastic materials that reduce cost, maintain structural integrity and allow for rapid deployment.
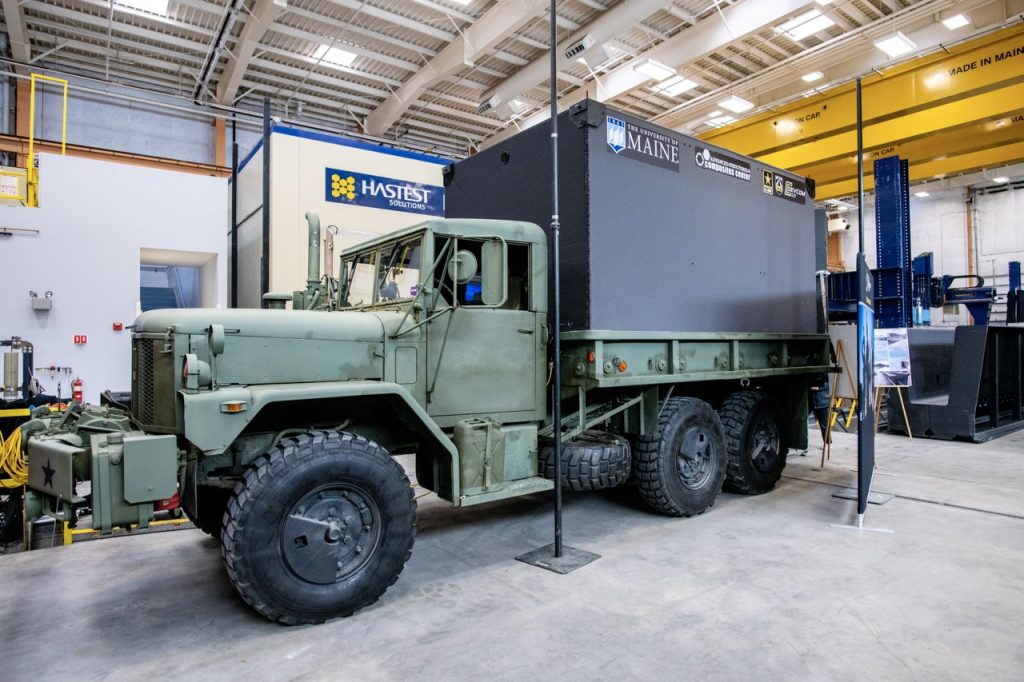
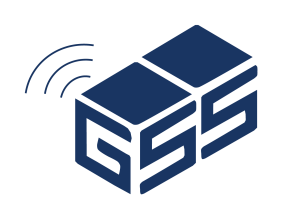