Materials Development
| Developing the next generation of environmentally sustainable structural thermoplastic composites that save energy, reduce waste, and allow for making parts faster, cheaper, and more reliably.
Materials development
| Developing the next generation of environmentally sustainable structural thermoplastic, bio and textile composites that save energy, reduce waste, and allow for making parts faster, cheaper, and more reliable.
CLIMATE SOLUTIONS
Thermoplastics
The Alfond Advanced Manufacturing Lab for Structural Thermoplastics was developed in 2015 to facilitate research in long-fiber reinforced thermoplastic composites. We are discovering mechanical properties, studying viscoelastic behavior during heating and forming, and performing computer-simulated modeling techniques for fiber-reinforced composite materials.
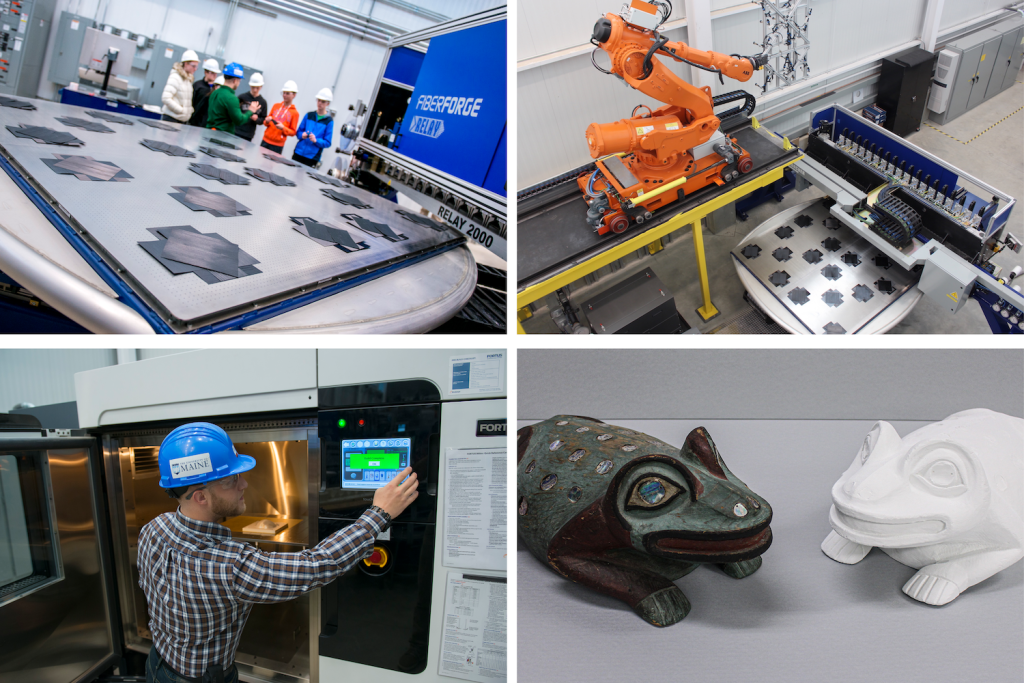
Research Areas
Composite-Concrete Beam
The Composite-Concrete Beam technology uses hybrid thermoplastics in which the beam is outfitted with welded shear studs. This research was commissioned by the Engineering Research and Development (ERDC) of the U.S. Army Corps of Engineers for the development of a stiffened panel system for use in load-bearing hybrid composite-concrete structures.

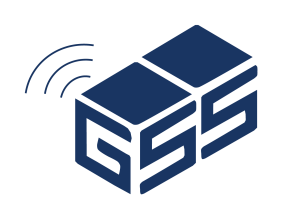
Global Secure Shipping
Global Secure Shipping’s (GSS) patented, durable and cost-effective technologies enable government and commercial companies to fight theft and tampering by Transnational Criminal Organizations and minimize loss of real and intellectual property.
Cultural Object Replication
In 2020, the Central Council of Tlingit and Haida Indian Tribes of Alaska requested that the University of Maine’s Hudson Museum return a 19th-century Tlingit frog clan helmet that was part of the museum’s collection. The Hudson partnered with researchers at the Advanced Structures and Composites Center (ASCC), as well as the Intermedia Department to create a 3D-printed replica of the helmet.
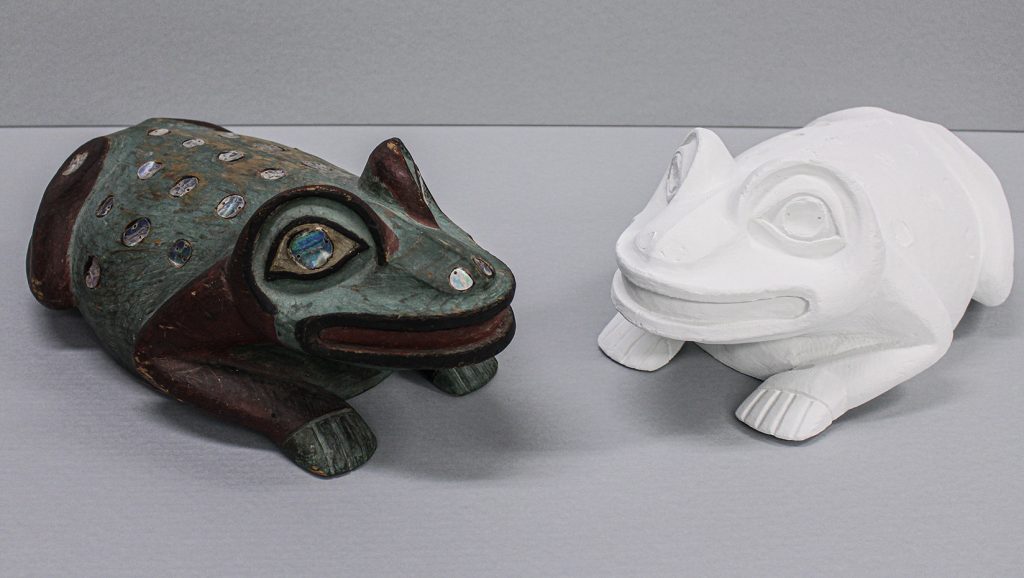
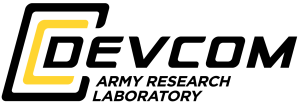
Lightweight Military Ground Vehicles
A partnership with the ASCC and US Army DEVCOM Ground Vehicle System Center was formed to develop technology to reduce the weight of military ground vehicles with fiber-reinforced thermoplastic materials that reduce cost, maintain structural integrity, and allow for rapid deployment.
The Continuous Forming Machine (CFM)
The CFM is a University of Maine-developed technology, based on pultrusion and thermoforming, used to manufacture complex thermoplastic Fiber Reinforced Polymer (FRP) parts. The CFM has allowed for the development of Hybridized Advanced Additive Manufacturing (HAAM), a novel manufacturing process that lowers additive manufacturing costs while boosting innovation potential.
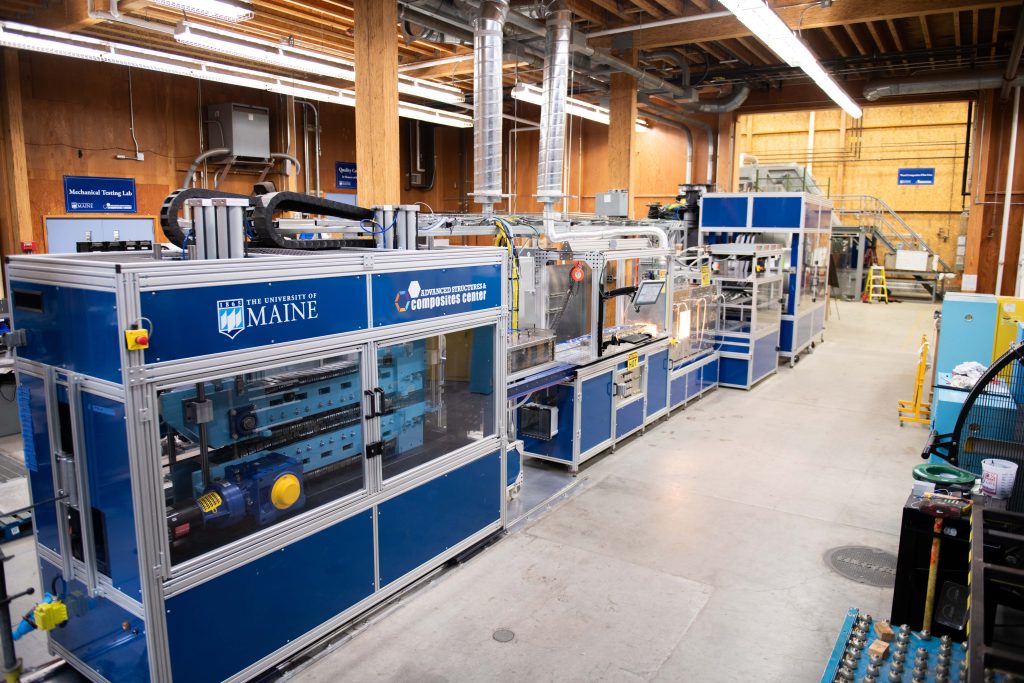
CLIMATE SOLUTIONS
Bio-Based Materials
The UMaine Composites Center is an ISO 17025 accredited testing laboratory with nearly 20 years of testing experience meeting industry standards from coupon-scale to full-scale. We have a successful history of partnering with industry and government, with over 500 product development and testing projects completed to date. Our facility includes fully equipped, integrated laboratories to develop and test durable, lightweight, corrosion-resistant material solutions for a wide variety of industries.
Our material property testing includes adhesives, composite materials, fasteners, plastic materials, structural, and wood products, among others.
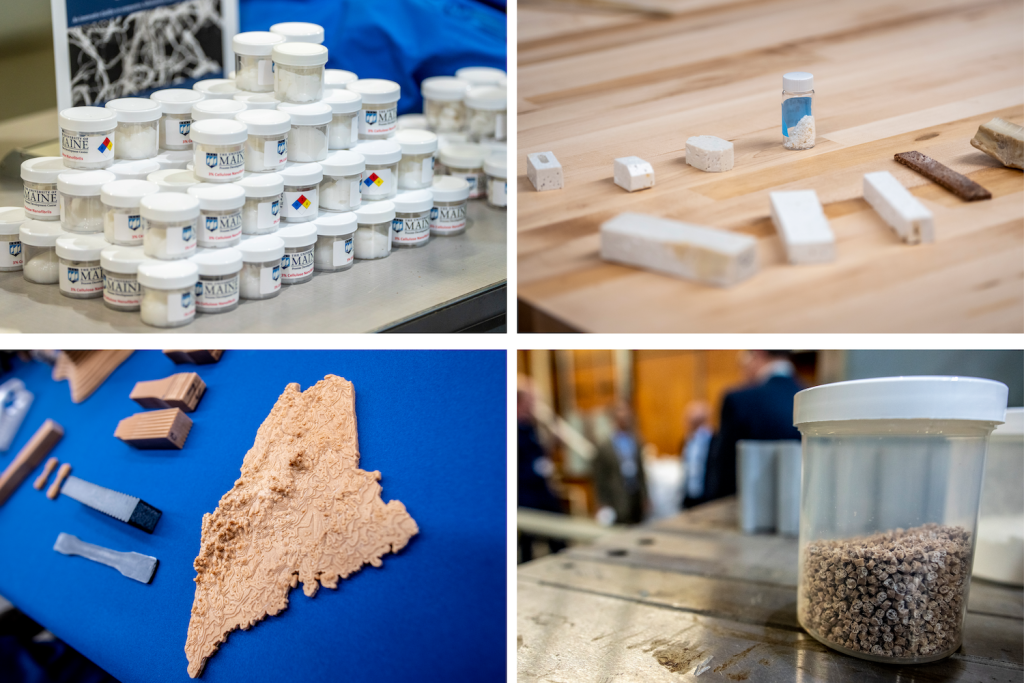
Research Areas
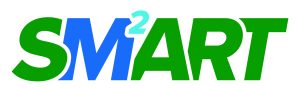
SM²ART
The Sustainable Materials and Manufacturing Alliance for Renewable Technologies (or SM²ART) is a collaborative initiative between the Department of Energy’s Manufacturing Demonstration Facility (MDF) at Oak Ridge National Laboratory (ORNL) and the Advanced Structures and Composites Center (ASCC) at the University of Maine (UMaine). The innovative research performed between these two world-class research facilities combined with industry guidance focuses on forest-derived bioproducts with an emphasis on large-scale additive manufacturing.
Material Development
The Our team is at the forefront of developing sustainable materials that cost less and require significantly less energy to produce. For example, we have reduced the energy needed to produce some of these materials by 44%, further reducing their carbon footprint by almost half.
We are improving the performance of bio-based materials to match or exceed the mechanical properties of similar fossil-fuel derived materials. For example, some of these bio-based composites show significant improvements in tensile strength and modulus, by 5.4% and 29.8%, compared to traditional materials.
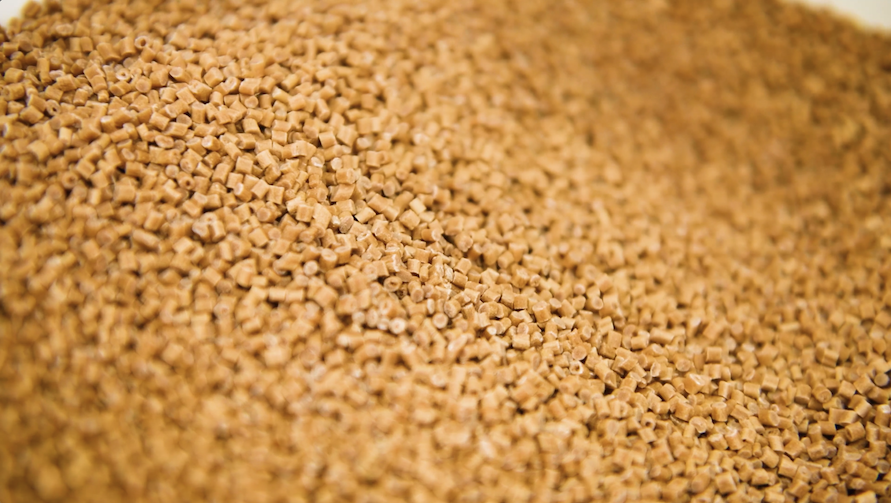
CLIMATE SOLUTIONS
Textiles
Textile Innovation: The Fiber and Specialty Textiles Research (FASTR) Lab
The FASTR Lab, a leading center for Fiber and Specialty Textiles Research within the University of Maine’s Advanced Structures and Composites Center (ASCC), drives textile innovation through a vertically-integrated approach from raw material development to comprehensive testing. Leveraging cutting-edge advanced manufacturing capabilities, FASTR specializes in novel fiber and yarn creation, advanced fabric production (including 3D weaving and knitting), functional coating and integration, and material compounding. As a large-scale digital additive and hybrid manufacturing test bed, FASTR partners with industry, government, and academia to accelerate technology maturation, support commercialization, and foster workforce development. This integrated effort, aligned with ASCC’s mission, significantly contributes to U.S. global competitiveness and well-being by developing revolutionary fibers and textiles for diverse applications, including defense, energy, and advanced consumer products, shaping a more resilient and sustainable future.
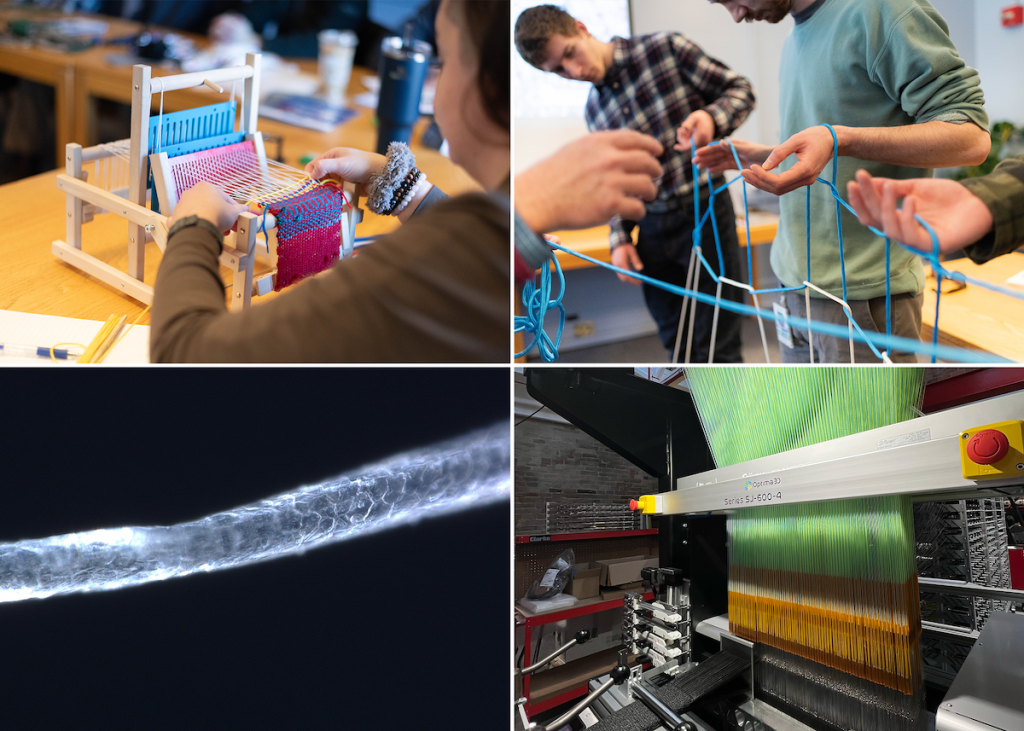