At the forefront of testing and manufacturing new, innovative, and sustainable forest products to revitalize and diversify Maine’s forest-based economy.
Strand Pilot Line
In order to attract and support fiberboard industries in the region, the establishment of a regional pilot-scale R&D facility is essential. The Strand Pilot Line helps to facilitate moving lab-scale research to a full-scale production plant faster and with less risk. In addition, a near industrial pilot plant helps develop products and processes for a production scale plant. Most pilot plants are multi-purpose and can minimize costly downtime of a mill’s manufacturing line.
The UMaine Advanced Structures and Composites Center Wood Composites Pilot Line allows for production of oriented strand board (OSB), laminated veneer lumber (LVL), particleboard, Wood Fiber Insulation, and other cellulosic composites on a near-industrial scale.
CAPABILITIES
EQUIPMENT
CONDITIONING
Log Soak Tank
STRANDING
Carmanah 12/48 Lab Strander
SCREENING
Acrowood Trillium & Diamond Roll combination screen
DRYING
Koch Bros. in-line conveyor forced-air dryer
Nyle dehumidification dry kiln
RESIN BLENDING
Large Coil Resin Blender
Small Coil Resin Blender
PRESSING
Dieffenbacher hot oil and/or steam injection press
4' X 8' ERIE MILL & PRESS
CONDITIONING & TESTING
The UMaine Composites Center, an ISO 17025 accredited testing laboratory, has a full suite of AST wood products testing capabilities within its accreditation scope (such as ASTM D143, D198, D1037, D4761, etc.).
CONTACT:
Russell Edgar
|Wood Composites Manager
RUSSELL.EDGAR@COMPOSITES.MAINE.EDU
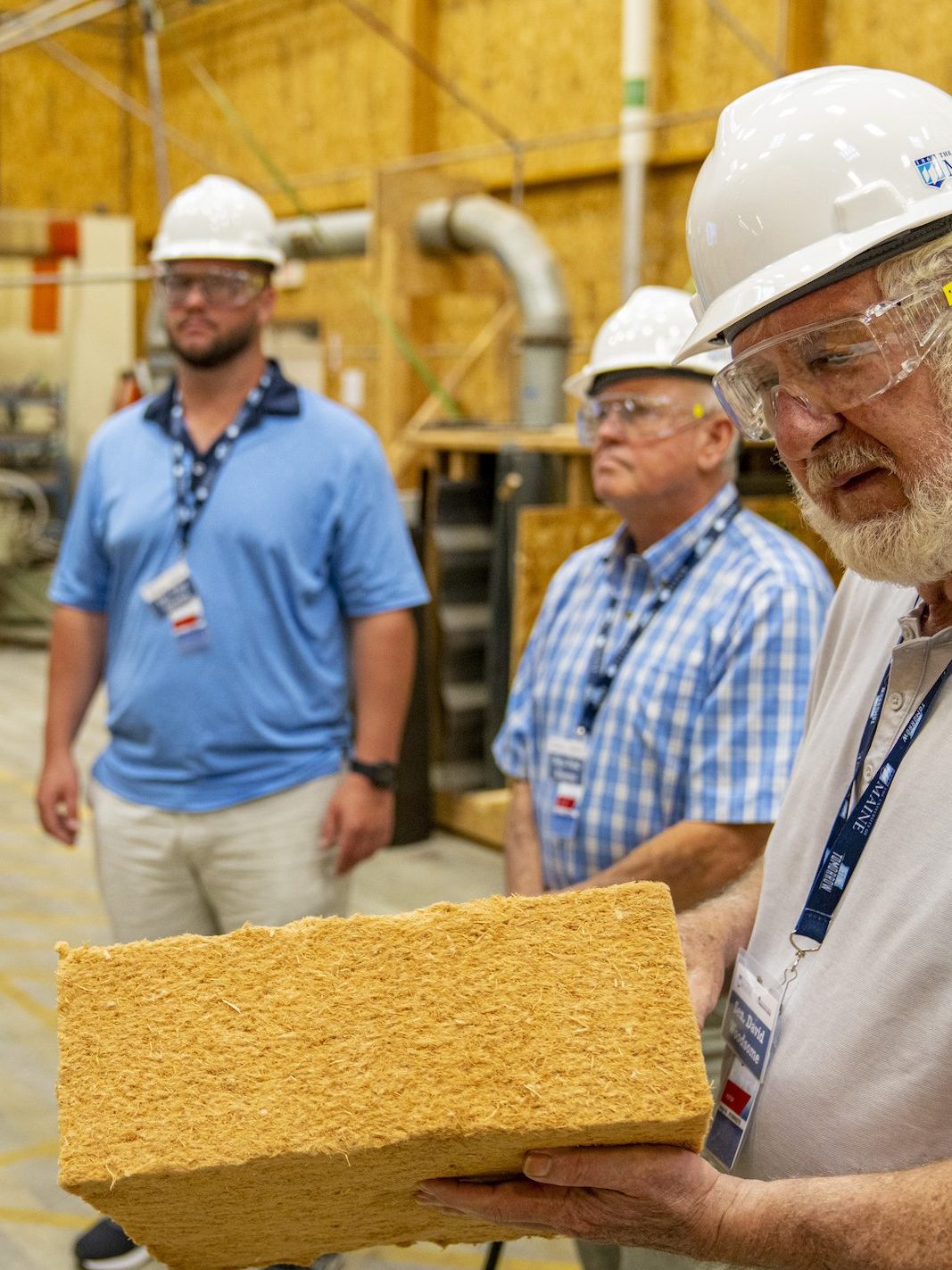
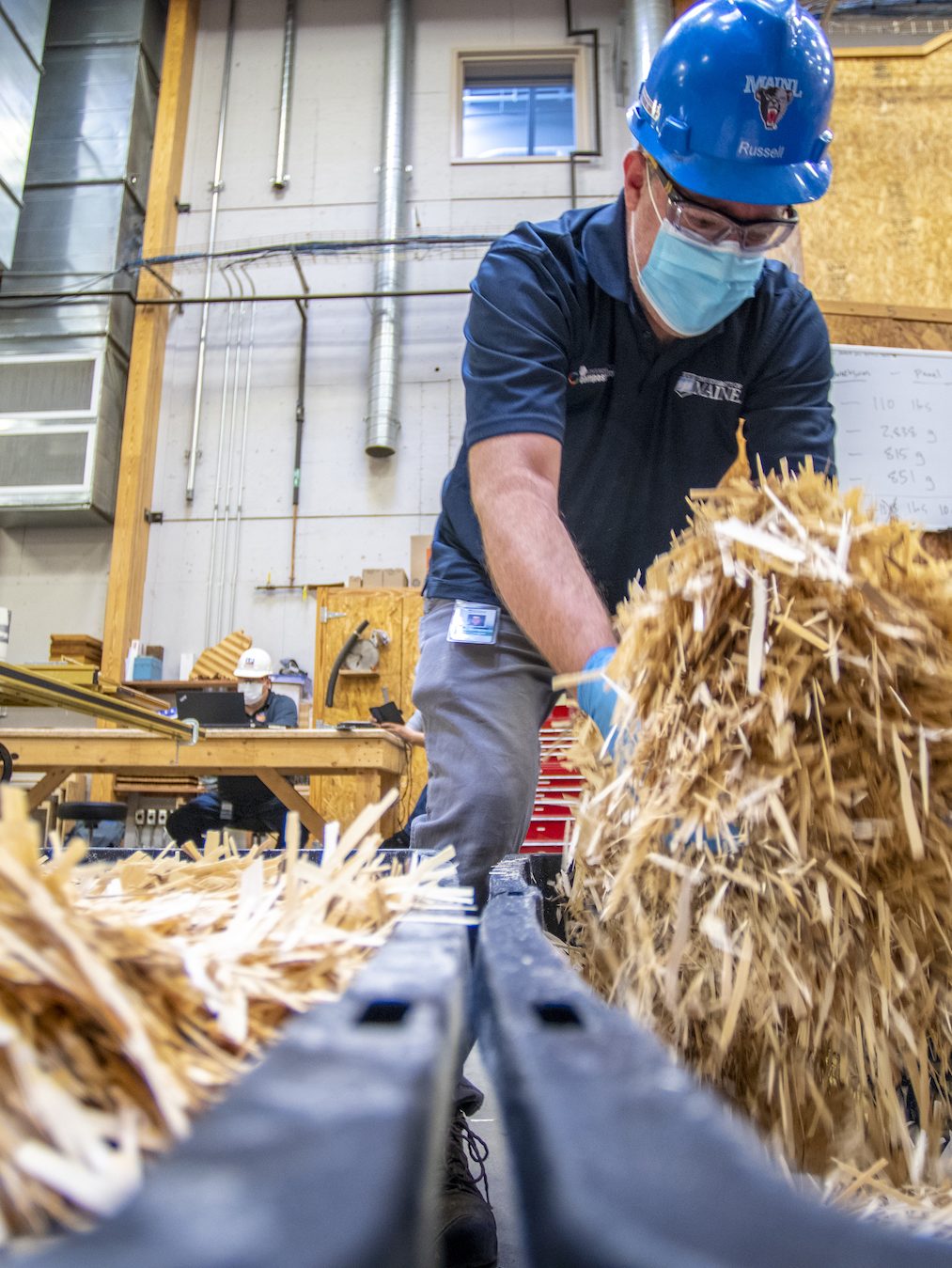
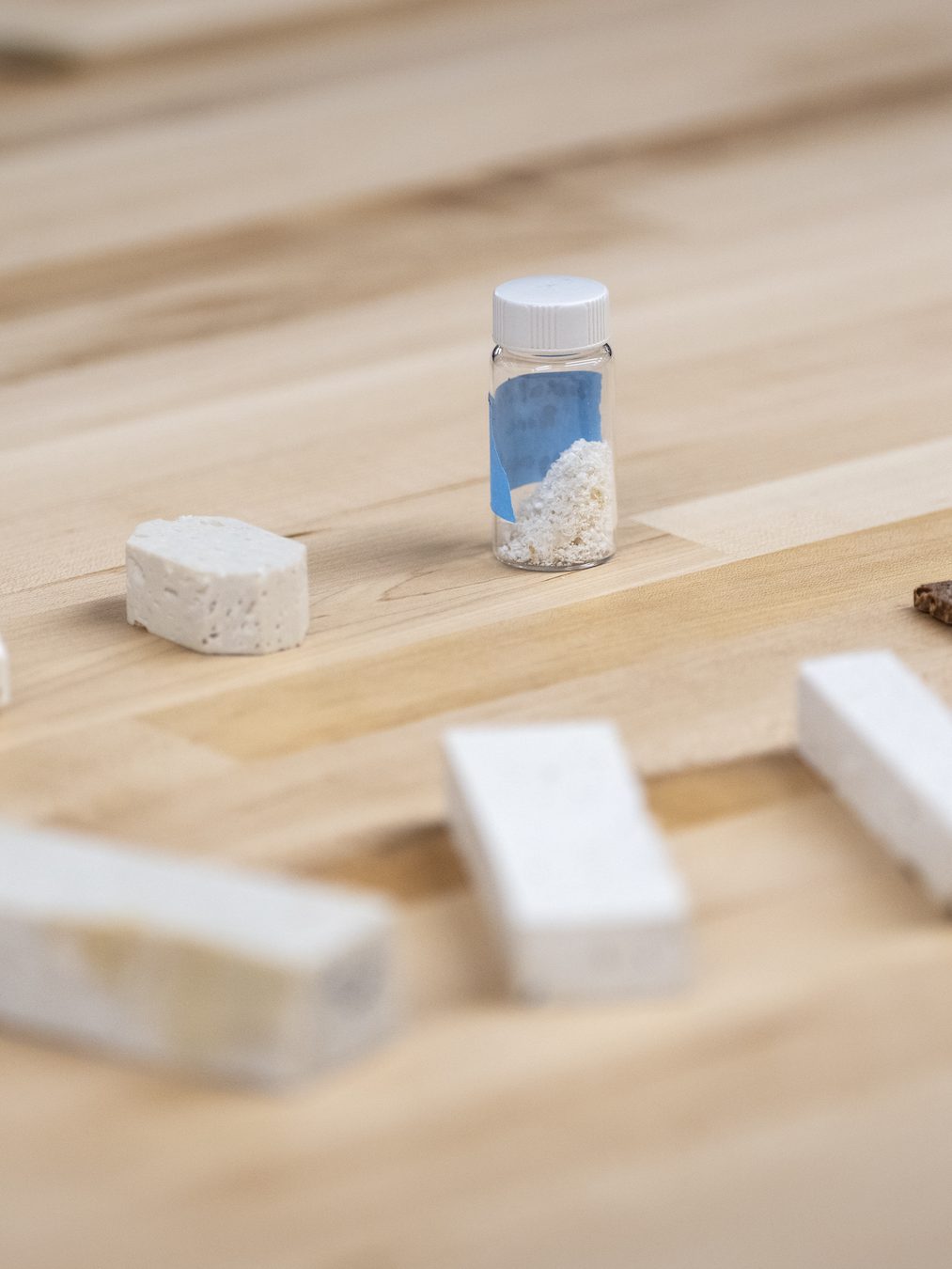
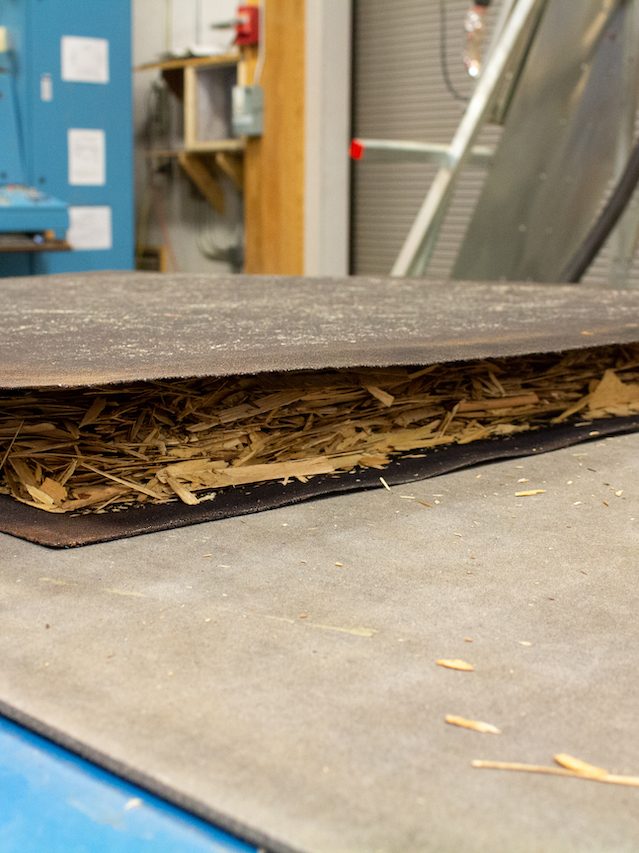
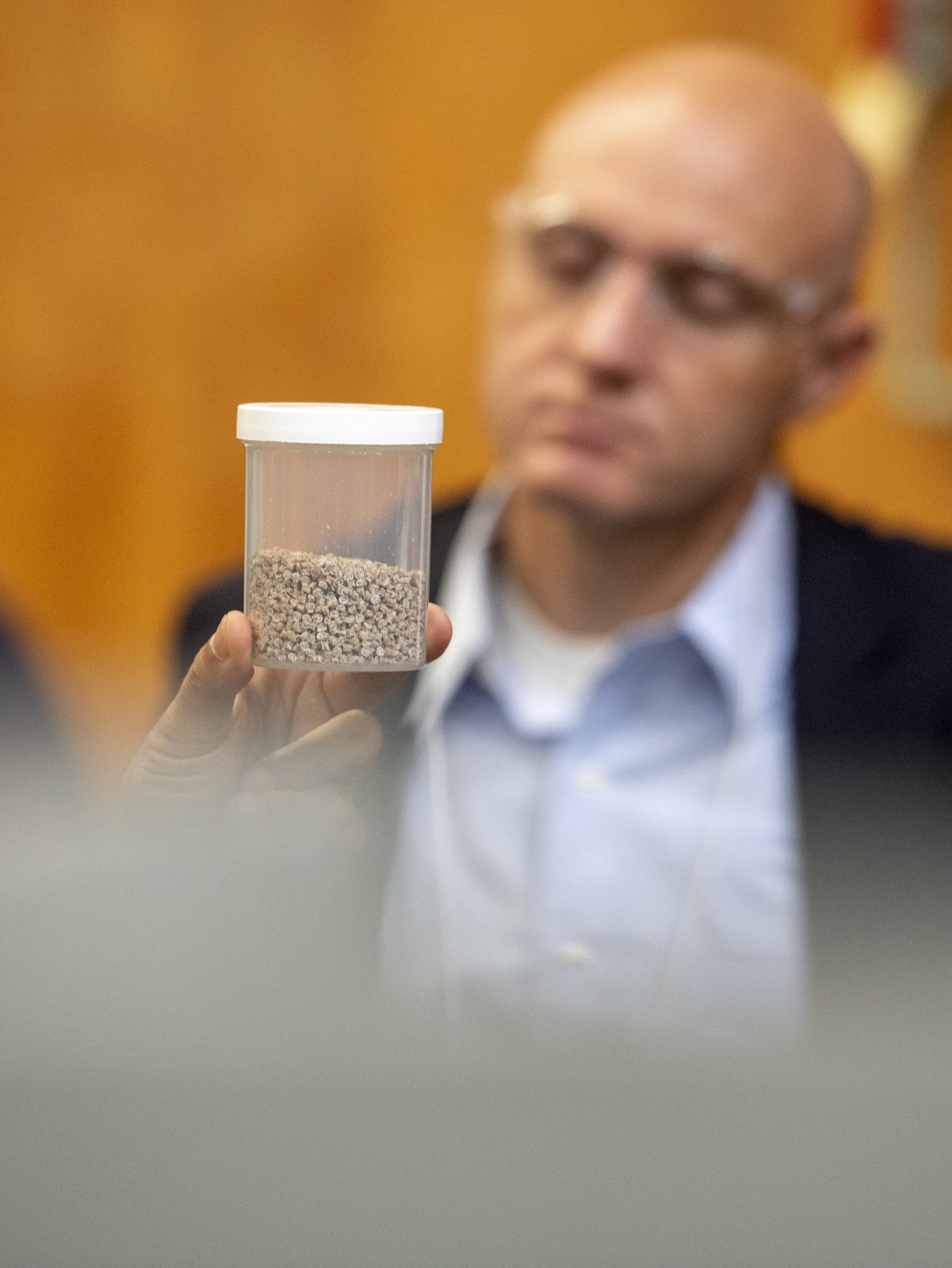
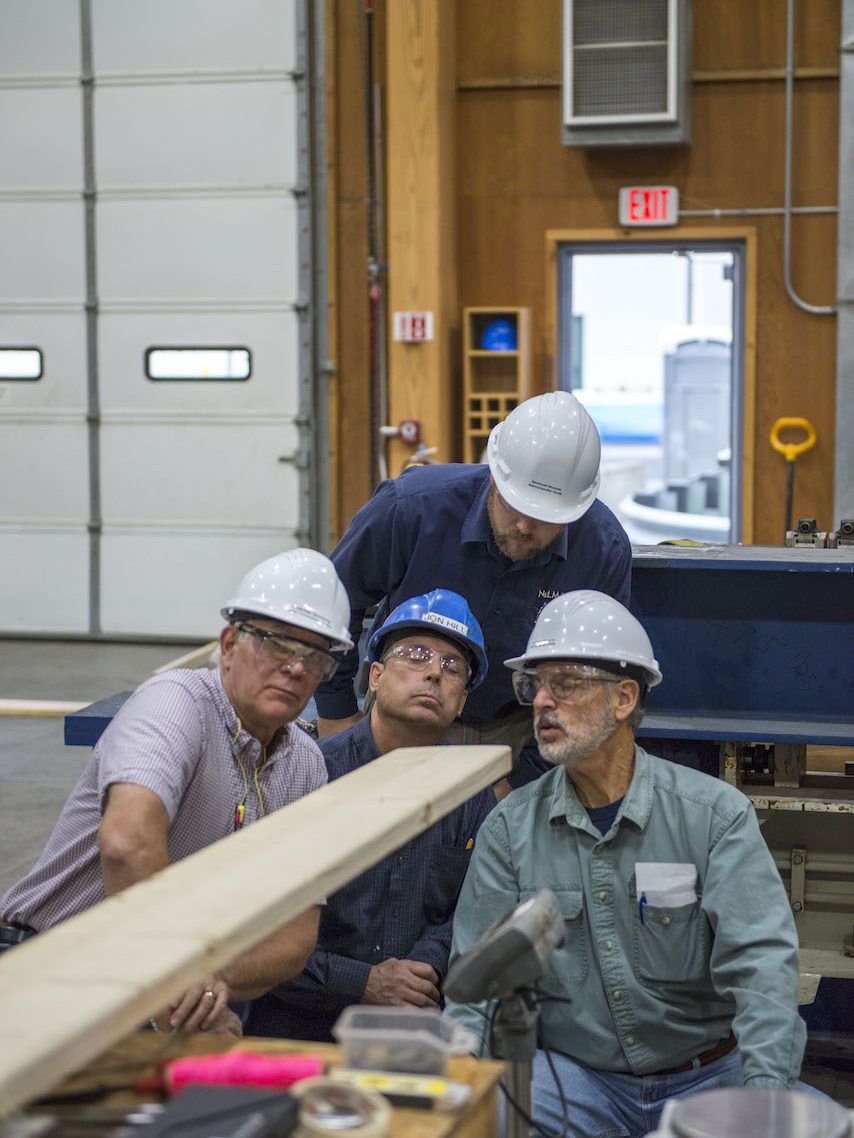