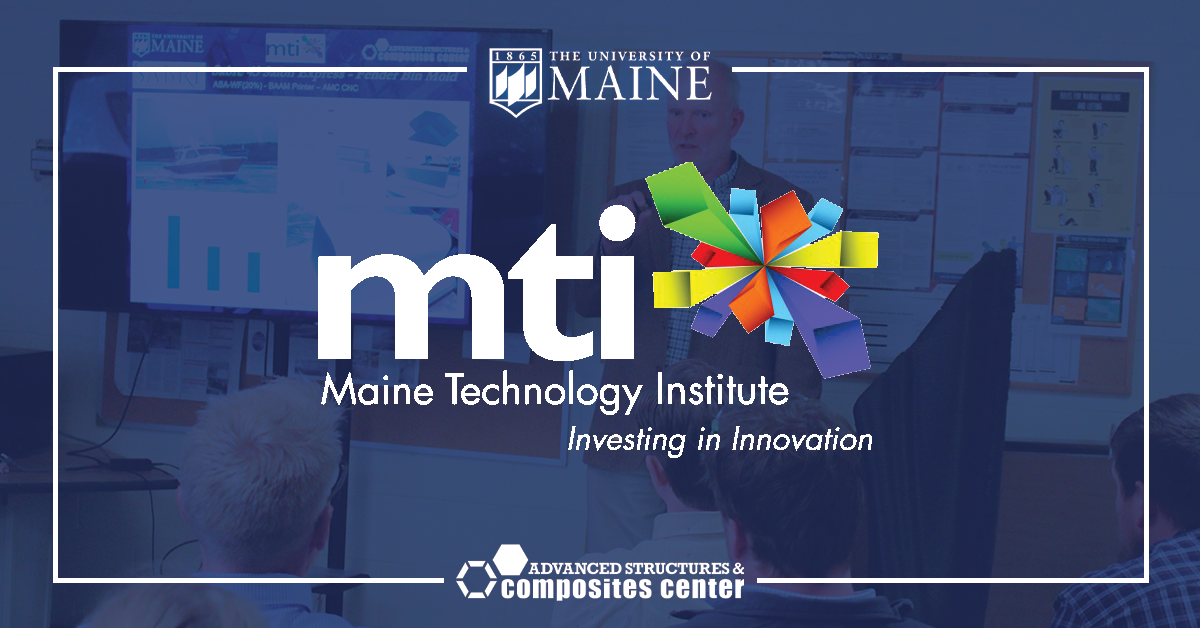
ASCC Paves the Way in Sustainable Marine Tooling
ASCC researchers, James Anderson and Dr. Andrew Gifford met with the Maine Technology Institute (MTI) Maine Boatbuilder tooling cluster, a consortium of representatives from the state’s boat-building and material-compounding industries, to present findings on a recently completed project. Funded by the MTI’s Cluster Initiative Program and with the assistance of some of Maine’s largest boat-building companies, this event marked the end of a $500k research and development program at the ASCC. This work was actively supported by Back Cove Yachts, Custom Composite Technologies, Hinckley Yachts, Hodgdon Yachts, Lyman Morse Boatbuilding, and Compounding Solutions.
Since 2019, the ASCC has been investigating the use of bio-based thermoplastics for marine tooling with an aim to not only produce reusable & recyclable molds for marine composite parts but to also investigate more sustainable materials to do so. During the project, many conventional and wood flour-filled thermoplastic materials were tested for use in marine tooling. The ASCC has a long history of working with wood-filled thermoplastics for the building industry through the work of Dr. Doug Gardner. This experience supported the development of low-cost, robust materials that can be 3D printed as alternatives to higher-cost engineering carbon-filled thermoplastics. The program delivered 14 mold sections made up of 6 composite molds that were 3D printed and CNC machined at the ASCC and was delivered to the MTI Cluster Boatbuilding partners for final finishing to their individual requirements. The ASCC supported numerous undergraduate students throughout the project while providing educational opportunities in 3D printing for boat builders and demonstrating that bio-based thermoplastics can be used to create marine composite tooling.
This event was the final dissemination of the project’s findings. It consisted of an in-depth presentation of the process used to redesign the molds for 3D printing, the cost analysis of the 3D printed molds, a museum-like display showing all of the completed prototype molds, and feedback from the cluster partners on their experiences using the molds. The afternoon concluded with a roundtable discussion between the ASCC researchers and the Maine Boatbuilders associated with the cluster, which included the initial thoughts and potential future applications of this technology. The molds all performed as expected with longer term use trials ongoing to understand the longevity of the molds. There was a broad positive consensus for the future of this technology and the commercialization of 3D printed tooling, including the use of bio-based thermoplastics.
The overarching conclusion was that 3D printing can be used to rapidly produce robust tooling for marine composite applications. The use of higher cost engineering grade thermoplastics is cost comparable with traditional tool manufacturing techniques. The use of wood-filled thermoplastics offers the opportunity to significantly reduce the cost of the materials whilst utilizing local materials with a lower carbon footprint. Moving forward, this research will work with Maine’s Forest Products providers to source materials suitable for local compounding to produce the feedstock for 3D printing. In parallel with this effort opportunities to spin off this technology into a local commercial entity are being evaluated.
Boatbuilding in Maine has deep roots and a long history of innovation. With the research being conducted at the ASCC in 3D printing of bio-based thermoplastics, Maine’s Boatbuilding tradition will have environmentally sustainable and cost-effective tooling options.
Contact: Taylor Ward, Taylor.Ward@maine.edu