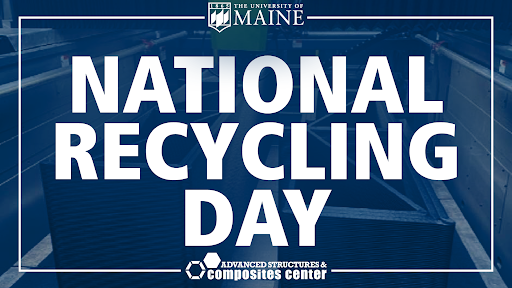
ASCC Celebrates National Recycling Day with a focus on the recycling of 3D printed concrete forms to reduce waste and improve sustainability in the transportation and construction industry.
November 15th is National Recycling Day, a day for recognizing the importance and impact of recycling and raising awareness about recycling and reuse activities. The Advanced Structures and Composites Center (ASCC) is dedicated to research innovation in green energy and materials for a more sustainable world, and many projects at the ASCC incorporate recycling and recyclable materials.
Today, we are highlighting two projects from ASCC researchers with the Transportation Infrastructure Durability Center that are investigating the recycling of 3D-printed concrete forms. Construction and demolition debris accounts for nearly 52% of waste in Maine landfills. Many of the materials used in construction can be reused, but in Maine, only about 2.5% of construction waste is recycled. Nationally, 600 million tons of construction and demolition materials were generated in 2018, more than twice the amount of municipal solid waste generated in the same year.
The application of this ASCC research has the potential to reduce waste and promote sustainability in the construction industry while lowering labor costs and extending the life of transportation infrastructure. In line with the ASCC’s Green Energy and Materials (GEM) strategic plan, this innovative research facilitates new ways of recycling at the intersection of advanced manufacturing, economic development, and transportation infrastructure solutions.
Recycling Large-Scale 3D-Printed Polymer Composite Precast Concrete Forms
Dr. Roberto Lopez-Anido, Dr. Sunil Bhandari, and Dr. Lu Wang are researching the recycling of 3D-printed precast concrete forms. As large-scale thermoplastic composite 3D printing is becoming more prevalent in industry, the printing of precast concrete forms is becoming a significant common practice. ASCC researchers have identified the potential to reuse and recycle the precast concrete forms; the thermoplastic composite can be recycled into feedstock pellets and used again for 3D printing newer parts. The recycling process for 3D-printed concrete forms is not well-established, and this project is investigating efficient ways of removing debris, cutting 3D-printed parts into smaller pieces, and pelletizing. Additionally, research will involve characterizing the degradation in material properties with each recycling, and comparing the cost of recycling to the cost of the 3D printed material.
Thermoplastic Composites by 3D Printing and Automated Manufacturing to Extend the Life of Transportation Facilities
Dr. Roberto Lopez-Anido and Dr. Sunil Bhandari are working with Dr. Douglas Gardner to study recent advances in 3D printing that expand the possibilities for making forms for precast concrete structures. The researchers are identifying applications for the large-scale 3D printing of forms and tooling for precast concrete parts in transportation, using bio-based fillers and reinforcements, and thermoplastic materials. The thermoplastic composite materials in 3D printed molds can be reprocessed and recycled, and this research project is evaluating the performance and durability of the molds with repeated casting and demolding, as well as the durability and dimensional tolerance of bio-based 3D printed forms. The ability to recycle the 3D printed forms and reuse the wood-filled thermoplastic material could be a capital asset for precasters and reduce labor costs. Furthermore, the technology can be implemented by the Departments of Transportation for use in transportation applications.
To learn more about the Transportation Infrastructure Durability Center at the ASCC, click here.
Contact: Katelin Moody, katelin.moody@maine.edu