The Continuous Forming Machine
| Empowering manufacturers to reach new markets with lightweight, anti-corrosive, and infinitely shapeable parts through continuous production of long-fiber thermoplastic composites.

Example Capabilities
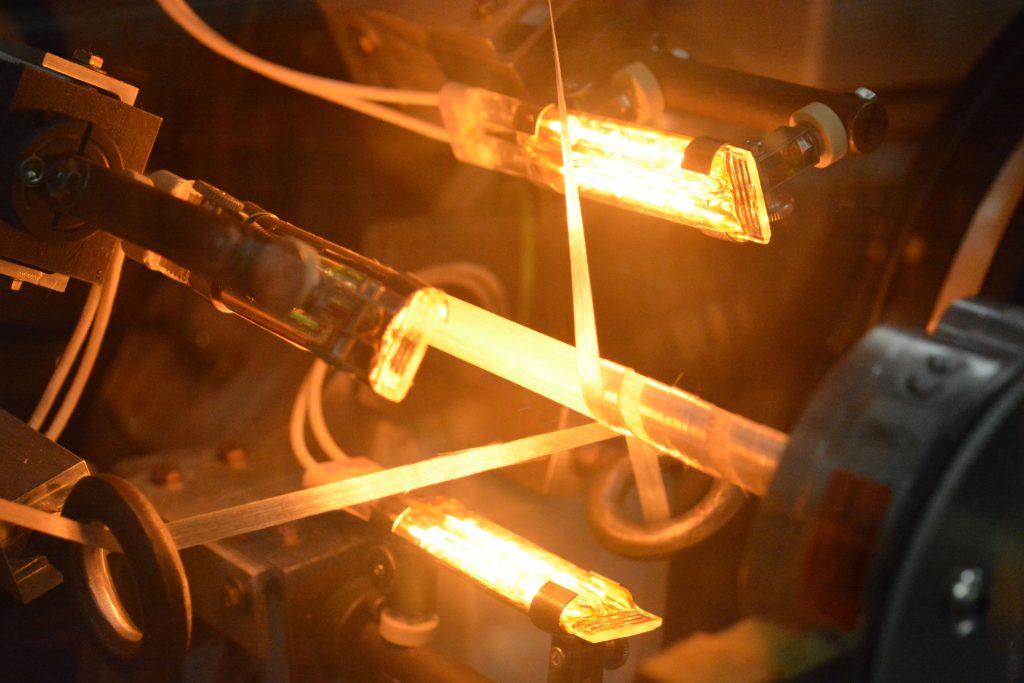
TECHNOLOGY
The Continuous Forming Machine (CFM) is a University of Maine-developed technology, based on pultrusion and thermoforming, used to manufacture complex thermoplastic Fiber Reinforced Polymer (FRP) parts. The CFM uses commercially available pre-saturated feedstocks such as UD tapes, fabrics, weaves, and more, which are heated to a viscous consistency and pulled/molded through a drive system – allowing for the creation of numerous thermoplastic parts.
Why Thermoplastic FRP?
Thermoplastic Resins
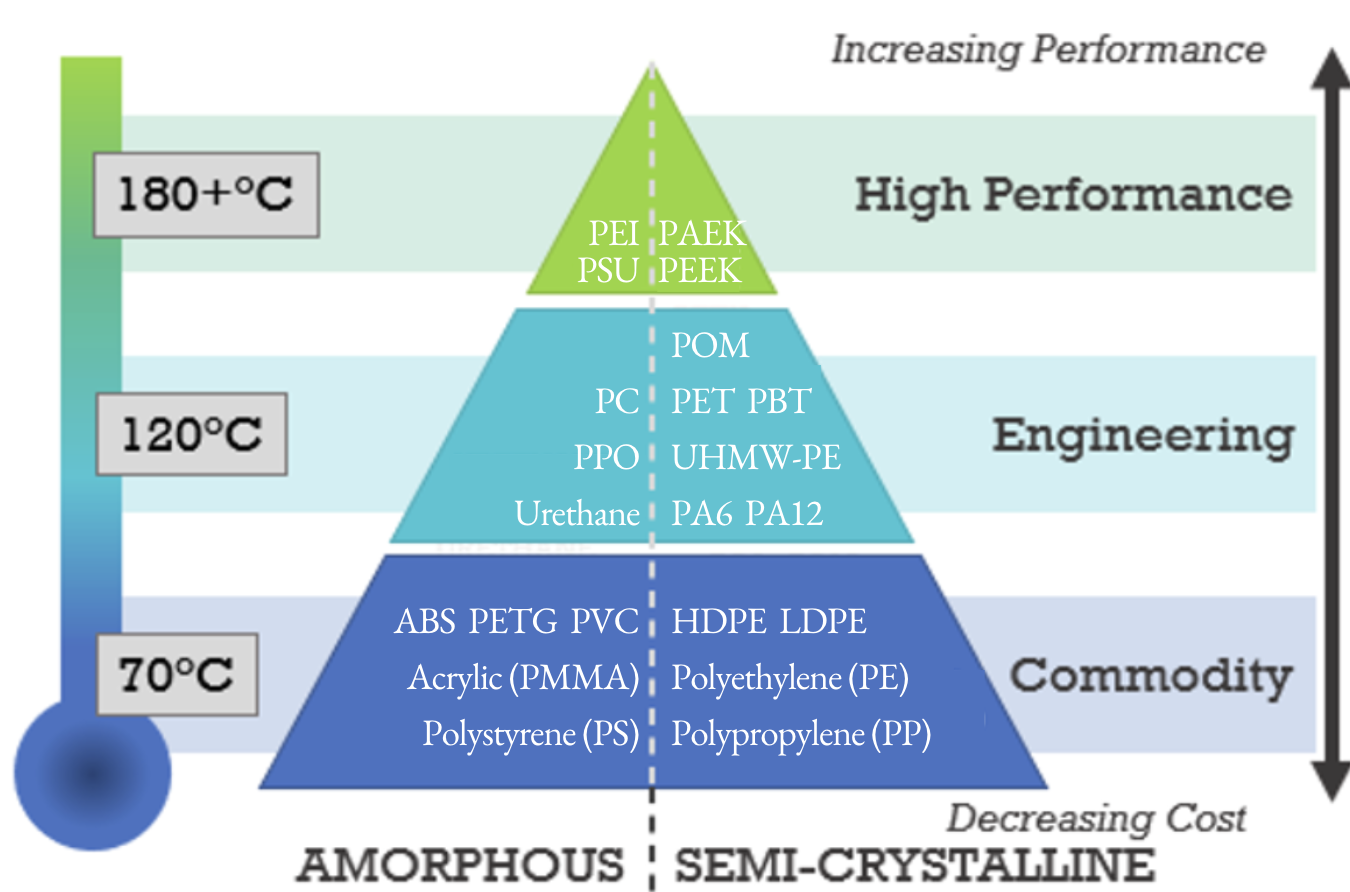
Impact of the CFM
CASE STUDY: Thermoplastic Composite Rebar
| A rebar with the same lightweight and corrosion-resistant properties as GFRP composite rebar, but it can be bent on-site and is fully recyclable.
Why Thermoplastic Composite Rebar?
Manufacturing with the CFM
The CFM is able to produce thermoplastic rebar at up to 12 ft/min. This process is fed by commercially available unidirectional UD tapes into a heating chamber. Any fiber selection can be used. Resin selection will be determined by ongoing durability studies. The thermoplastic material is then cooled and pulled through into the rebar shaft shape while also molding the rebar corrugations. ASCC is preparing rebar to meet requirements from ASTM, ACI, and AASHTO.
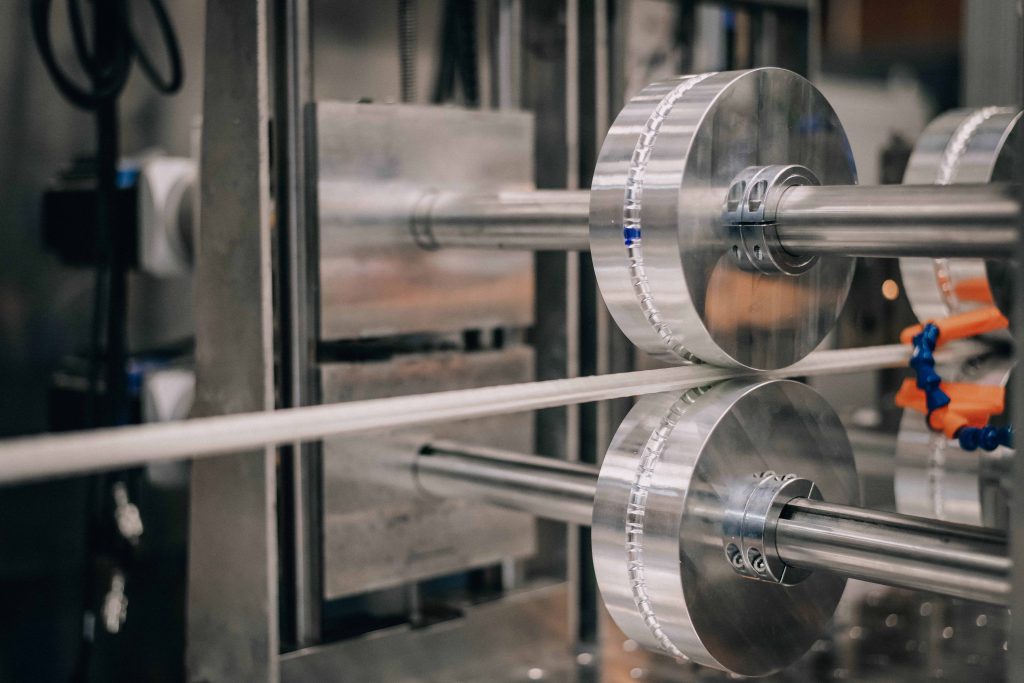
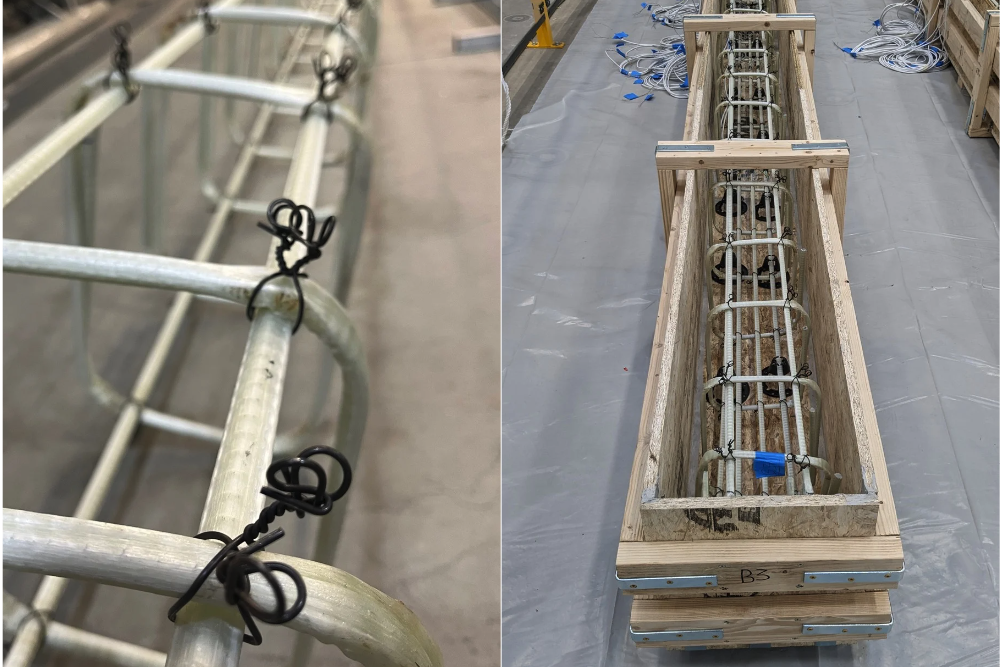
Thermoplastic Rebar Benefits
Unique Manufacturing Processes
| The development of the CFM has opened the door for novel composites manufacturing processes
Thermoplastic Composite Periodic Multi-Curvature Surfaces (TCPMCS)
TCPMCS allows for the creation of structural surfaces with minimal material by optimizing the placement and shape of materials to meet performance goals.
Expanding CFM Capabilities
TCPMCS Applications
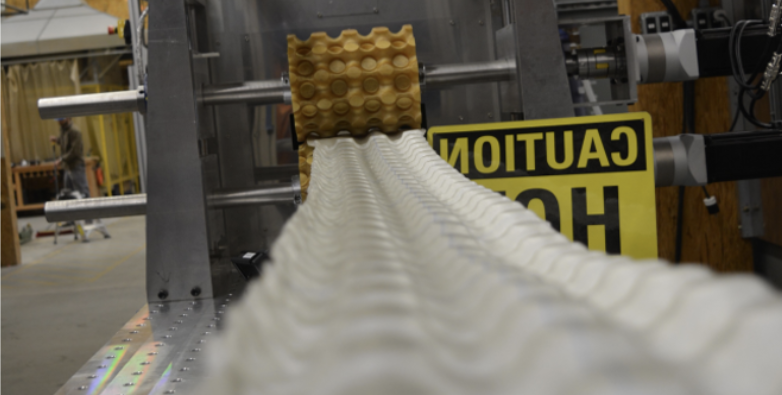
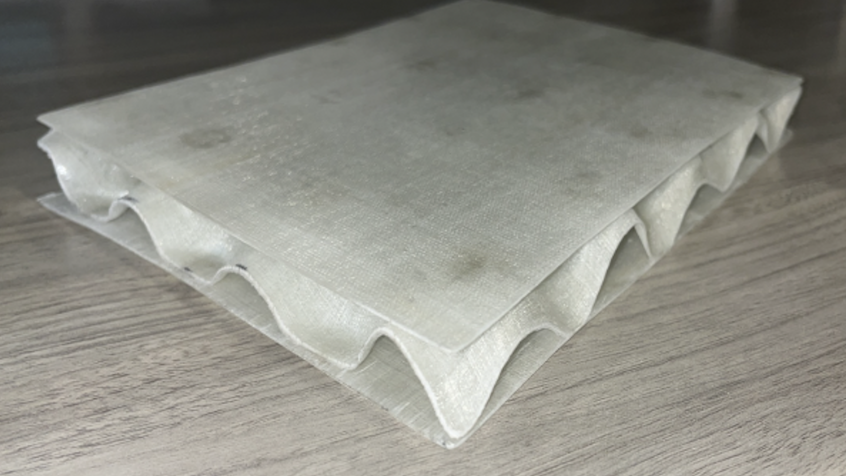
Hybridized Advanced Additive Manufacturing (HAAM)
HAAM lowers additive manufacturing costs while boosting innovation potential by integrating CFM-pultruded Continuous Fiber Reinforced Thermoplastic (CFRT) structural components with Large Scale Additive Manufacturing (LAAM). It enables the production of complex, cost-effective end-use thermoplastic parts and structures.
Why Hybridize?
HAAM Key Takeaways
Future HAAM Development
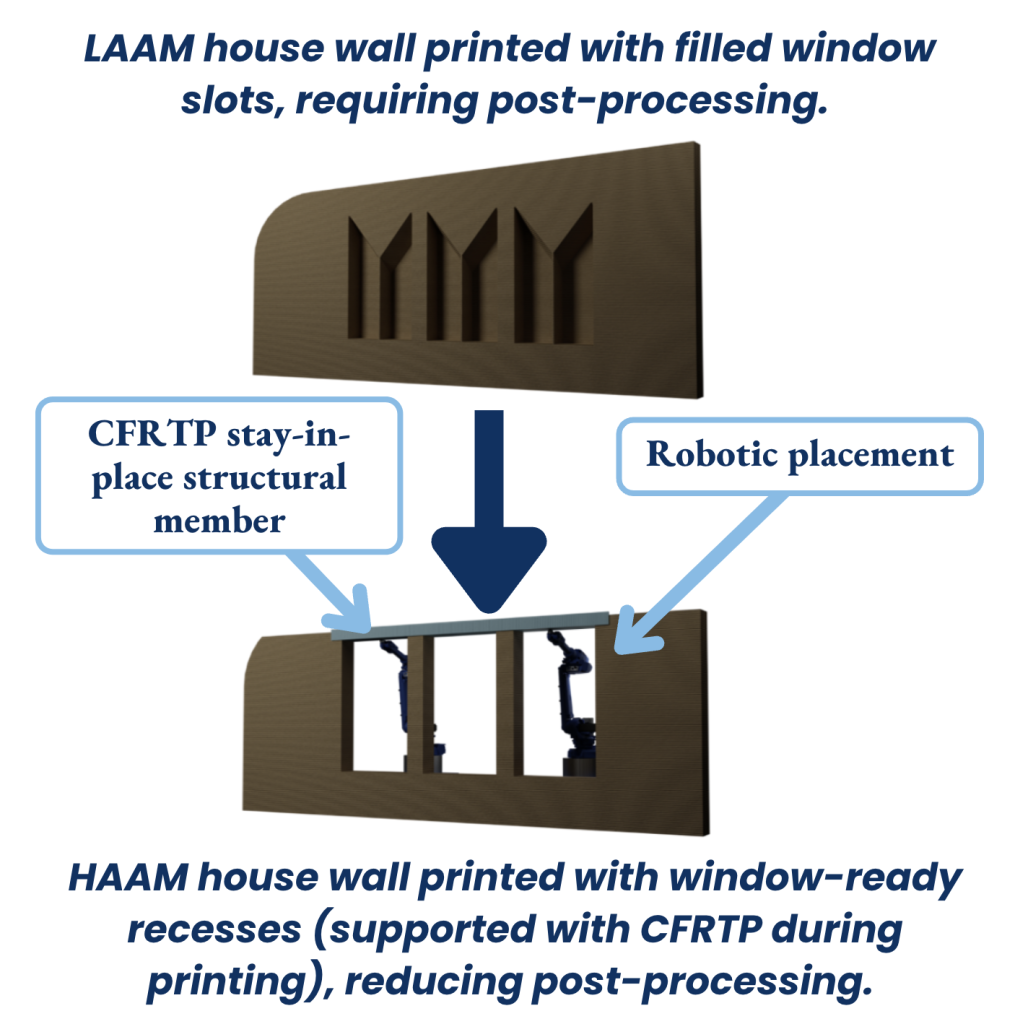
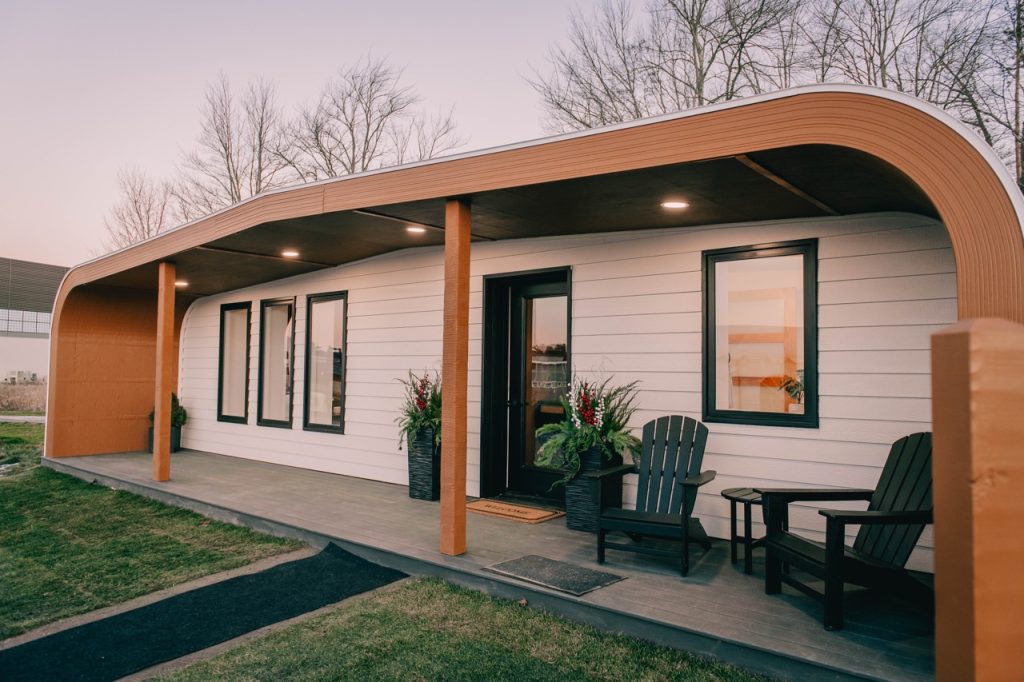