BioHome3D
| BioHome3D is the first 3D-printed house made entirely with forest-derived, recyclable materials

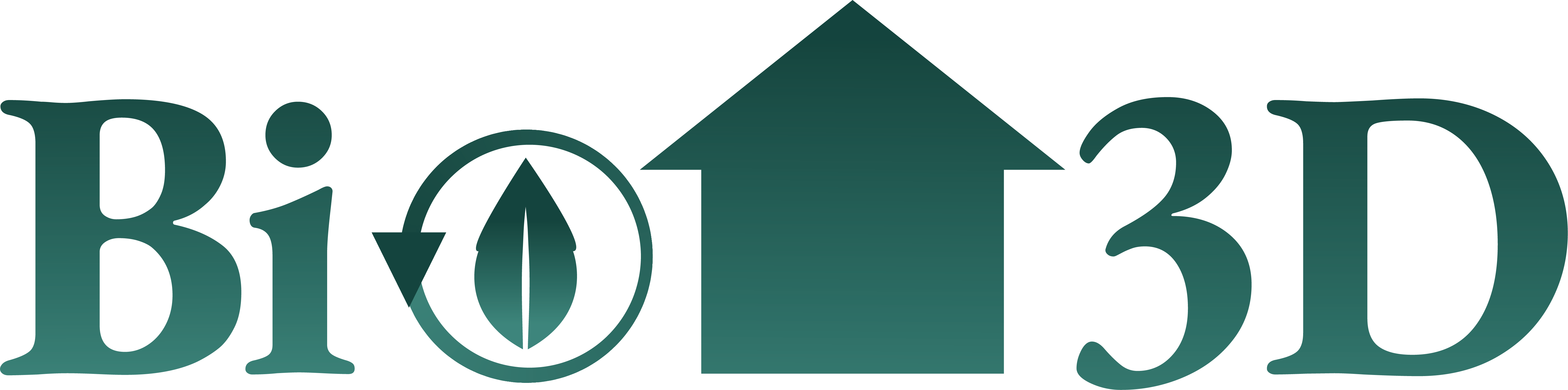
Unveiled November 21, 2022
TECHNOLOGY
Designed to address labor shortages and supply chain issues that are driving high costs and constricting the supply of affordable housing. Less time is required on-site building and fitting up the home due to the use of automated manufacturing and off-site production. Printing using abundant, renewable, locally sourced wood fiber feedstock reduces dependence on a constrained supply chain.
DEVELOPMENT
INNOVATION
World’s first 100% forest-derived house.
600 square foot single-family home
Technical R&D efforts leading to BioHome3D
MEDIA GALLERY
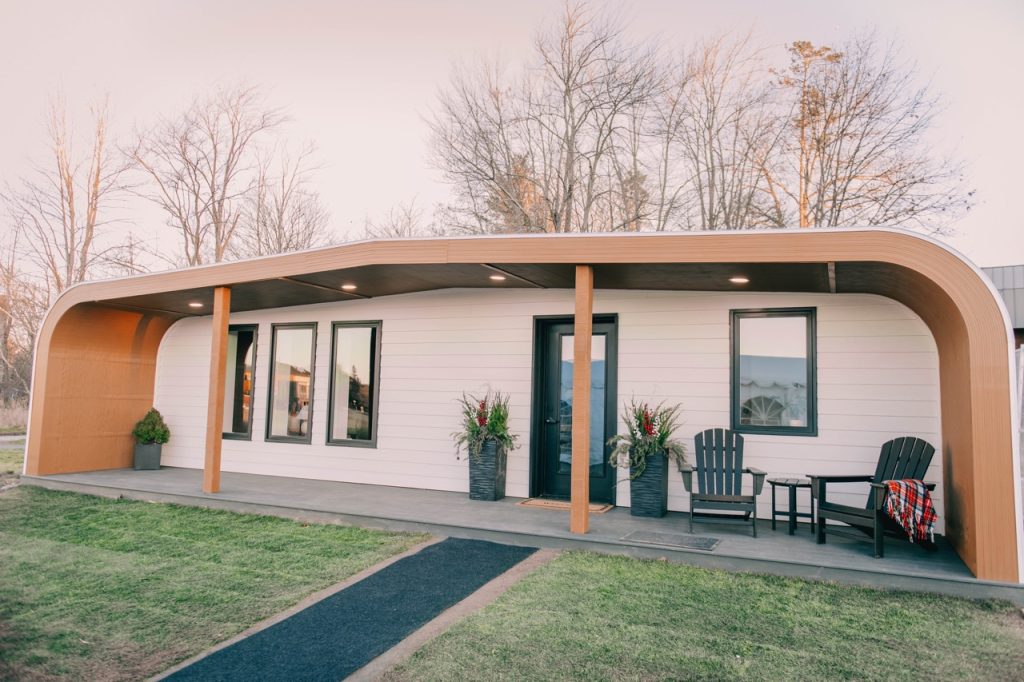
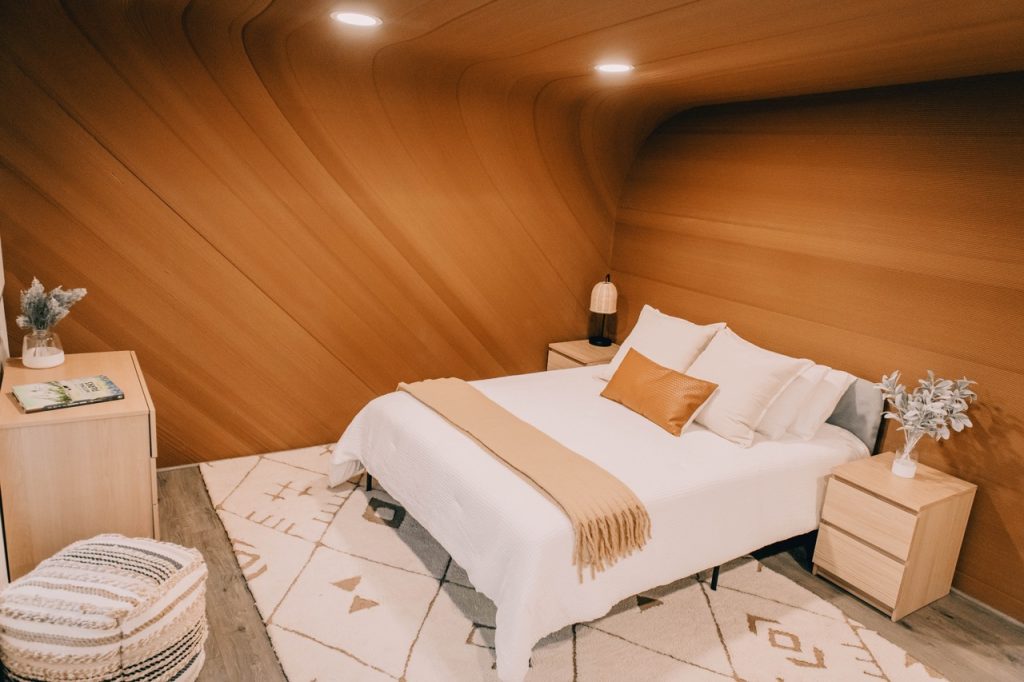

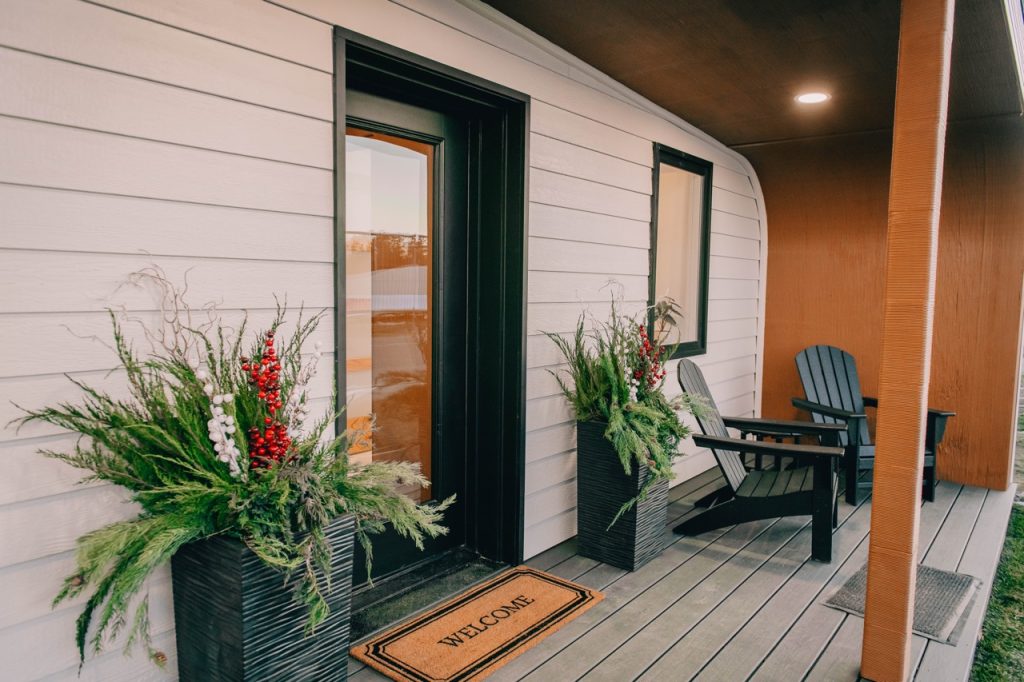
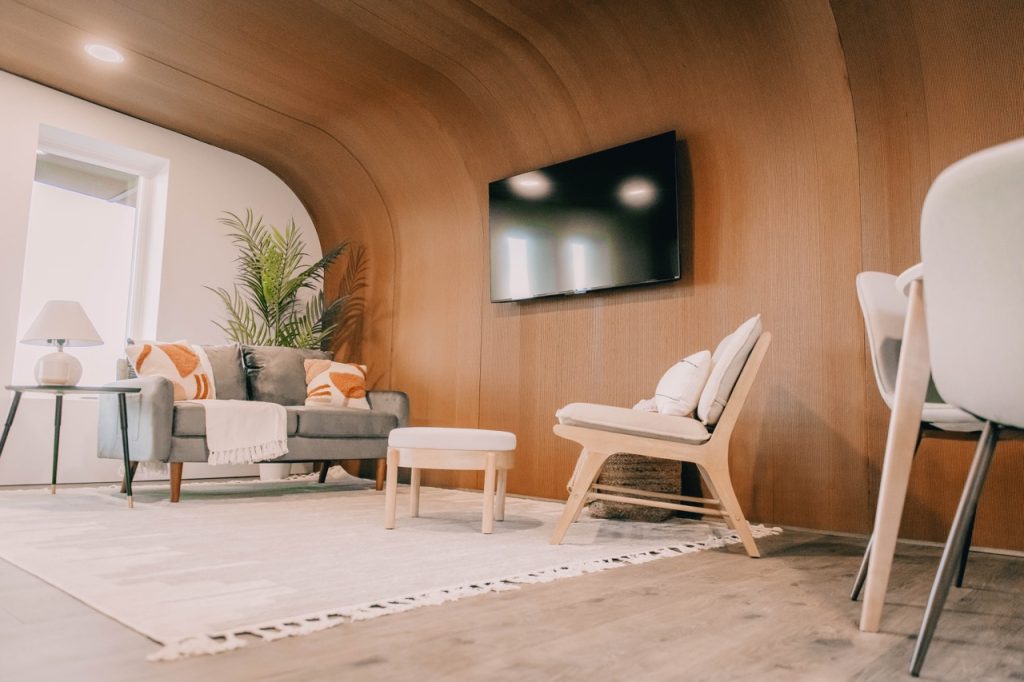
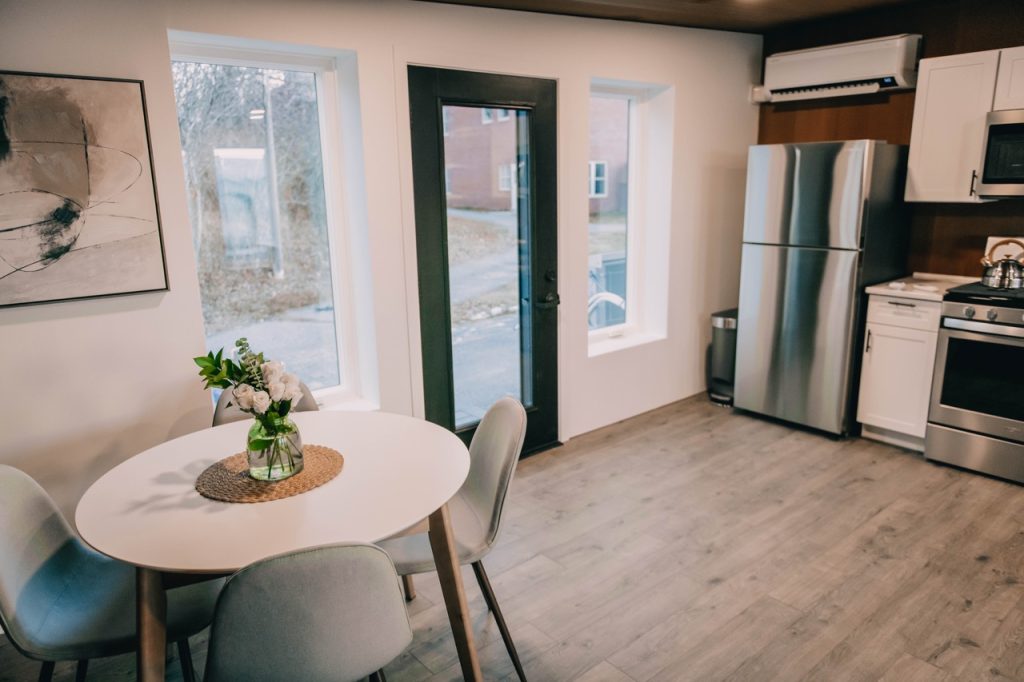
Thank you to our project partners
